Çok nadir istisnalar dışında, her tür şaftın işlenmesi, merkezleme makinelerinin kullanımına dayanır ve bu durumda, teknoloji aşağıdaki işlemlerden oluşur: iş parçalarını kesme, uçları düzeltme ve merkezleme, ardından tornalama işlemleri gerçekleştirilir. merkez torna tezgahları, çoğunlukla standart tipte çoklu kesicilerde, iş parçasını döndürdükten sonra, oluk açma işlemi gerçekleştirilir ve daha sonra tüm taşlama işlemleri, kamaların frezelenmesi en sık şaft taşlama işlemlerinden önce gerçekleştirilir.
Her şeyin sonundan sonra mekanik işleme miller kenarların sıkılması nedeniyle taşlamadan sonra genişlikteki bozulmaları nedeniyle kama yollarının sıhhi temizliğinin yapılması gerekir. Bu nedenle, bazı fabrikalar, özellikle kama kanalları mil taşlandıktan sonra yapılıyorsa, kama yollarını frezelemeyi tercih eder. Bu durumda, bir miktar kenar kaldırma nedeniyle, manuel bir soyma işlemi, yani pah kırma yapılması da gereklidir, ancak bu işlem ilk duruma göre daha az zahmetlidir, ayrıca sıyırma sırasında şaftın hasar görme riski azalır. .
Milin tüm dönüşleri yapılır, kural olarak, çok kesicili torna tezgahlarında iki kurulumda, her kurulum için milin bir kısmını döndürün. Ek olarak, şaftın tasarımına ve ekipmanın durumuna bağlı olarak, bazen şaftın ince tornalanmasını ve yiv uçlarının düzeltilmesi de dahil olmak üzere bitirme işinin doğasında olan birkaç kısa torna işlemini de gerçekleştirirler. filetolar, oluklar vb.
Oluklu haddeleme işlemi genellikle düzenli olarak gerçekleştirilir torna, özel bir tutucuya sabitlenmiş bir veya iki tırtıllı silindir yardımıyla. Silindirler, tek geçişte tam profilli bir oluk oluşturulacak şekilde mile karşı preslenerek uzunlamasına beslemede haddeleme gerçekleştirir.
Taşlama işlemleri geleneksel merkez silindirik taşlama makinelerinde üretilmektedir. Çoğu yüzey, ürünün tekerleğe göre uzunlamasına hareketi ile taşlanır ve sadece bazı durumlarda kullanılan enine beslemeler ile işlenen yüzeyin genişliğine göre geniş daireler ile taşlama daha verimli bir yöntemdir.
Freze kamaları basit yatay olarak üretilen freze makineleri... Küçük, manivelalı el tipi freze makineleri, kama yuvalarının üretiminde büyük başarı ile kullanılmıştır. Basitliklerine ve ilkel olmalarına rağmen, bu tür freze makineleri, bu tür kısa süreli operasyonlar için çok uygun ve yüksek verimlidir.
Uzun ve ince şaftların imalatında, taşlamadan önce, manuel veya mekanik tahrikli preslerde veya küçük hidrolik veya pnömatik preslerde gerçekleştirilen bir pansuman işlemi uygulanır. Üretim sürecindeki tüm boyutların kontrolü, katı limit ölçerler ve şablonlar kullanılarak gerçekleştirilir. Salgın kontrolleri ve doğrultma işlemleri dışında, gösterge cihazları neredeyse hiç kullanılmamaktadır.
Açıklanan teknolojinin dezavantajları esas olarak aşağıdaki gibidir::
1) kullanılan ekipman ve üretim yöntemleri düşük verimliliğe sahiptir ve modern seri üretim yöntemlerinin gerisinde kalmıştır;
2) Çoğu durumda, çelik, siyah kalibre edilmemiş çubuklar şeklinde bir başlangıç malzemesi olarak kullanılır, bu da şaftın en büyük çapa sahip olan orta kısmının da taşlanması ihtiyacına yol açar. Bu durum tek başına işlemenin karmaşıklığını artırarak en az %15-20 oranında maddi kayıplara yol açar;
3) iş parçasının kesilmesi, uçların döndürülmesi ve merkezlerin delinmesi işlemleri, seri üretimde çalışmak üzere tasarlanmış ve bu nedenle düşük verimliliğe sahip, nispeten büyük bir üretim kapasitesine sahip geleneksel ekipman üzerinde gerçekleştirilir. spesifik yer çekimi manuel yardımcı zaman. Bu nedenle, örneğin, merkez delme en sık olarak dikey delme makinelerinde iki geçişte, yani şaftın her bir tarafı bağımsız olarak şaftı döndürerek gerçekleştirilir;
4) tornalama işlemleri de yetersiz üretken evrensel ekipman üzerinde gerçekleştirilir. Kullanılmış çok kesicili makinelerin özel bir dezavantajı, ayarları bir standart şaft boyutundan diğerine hızlı bir şekilde değiştirmeye düşük adaptasyon kabiliyetleridir, bu da geçişler sırasında büyük zaman kayıplarına yol açar. Uygulanan oluklu üretim yöntemine özel dikkat gösterilmelidir. Torna tezgahlarında önceden işlenmiş milleri haddelemenin mevcut yöntemiyle, çapların boyutlarını yeterince doğru tutmak ve boyutlarda kabul edilemez dalgalanmalardan ve olukların gerekli düzlüğünden sapmalardan kaçınmak imkansızdır. İkincisi, rotor çekirdeğinin (armatür) doğru oturması için gereklidir. Son olarak, uzunlamasına beslemeli dar taşlarla uygulanan taşlama yöntemi etkisizdir. Kural olarak, örneğin boyunları taşlarken olduğu gibi, oldukça mümkün ve rasyonel olduğu durumlarda bile, makinelerin çalışma sırasında taşlanacak boyutları ölçmek için cihazlarla donatılmadığına dikkat edilmelidir. makinenin uçması, ancak boyutların kontrol edilmesi için makinenin durduğu.
Mevcut teknolojinin, işleme sırasında, özellikle son taşlamadan önce ve bitmiş formda şaftın temizlenmesini ve yıkanmasını sağlamadığına dikkat edilmelidir. En yaygın şaft merkezleme işlemi böyle görünür.
Ancak merkezsiz şaft işleme için tamamen farklı bir süreç vardır. Merkezleme yöntemine göre bir takım avantajlara sahip olan ve işleme karmaşıklığında önemli bir azalmaya yol açan . Bu işlem, otomotiv elektrik ekipmanlarının imalatında şaft imalatında büyük başarı ile kullanılmaktadır.
Merkezsiz yöntemle, başlangıç malzemesi mutlaka kalibre edilmiş ve dikkatlice düzleştirilmiş bir çubuk olmalıdır. İlk işlem - milin tamamen döndürülmesi bir çubuk makinesinde gerçekleştirilir. Uzun millerin taşlama sırasında bükülmesini önlemek için, miller merdane yatakları ile desteklenir. Millerin işlenmesine ilişkin sonraki işlemlerde ön taşlama, puntasız taşlama makinelerinde, ilk işlemler ise birbirini izleyen iki veya üç makinede ürünlerin beslemesi ile gerçekleştirilir.
Gelecekte, oluklu haddelenmiş... Otomotiv elektrik ekipmanlarının üretimindeki bu işlem, diğer elektrikli makine imalat tesislerinde yapıldığından farklı olarak gerçekleştirilmiştir. Çapların doğru boyutunu sağlamak ve çeşitli millerde aynı presleme gücünü korumak için, miller haddelemeden önce çapları boyunca taşlamaya tabi tutulmalı ve boyutlar üçüncü doğruluk sınıfına göre korunmalıdır. Yuvarlama işlemi, güçlü bir yatay diş ovalama makinesinde gerçekleştirilir. Bu haddeleme yönteminin çok yüksek üretkenliğine ek olarak, bazı makine tasarımlarında kesinlikle gerekli olan ondülasyonun tam düzlüğü de sağlanır.
Aslında, rotor göbeği oluklu bir şaft üzerine bastırılırsa, o zaman presleme işlemindeki bireysel tabakaları kaçınılmaz olarak ondülasyonun şeklini ve yönünü takip etme eğilimindedir. Bu nedenle, oluklar en azından çok hafif eğrilere sahipse ve dik bir spiral izliyorsa, o zaman çekirdekteki tüm oluklar olukların eğriliğini tekrar etmelidir.
Oluk şeklindeki bozulmaların, özellikle armatürün makine sarımı ile tamamen kabul edilemez olduğu bilinmektedir. Bir elektrikli makinenin armatürünün eğik oluklara sahip olması gerekiyorsa, olukların da karşılık gelen bir eğime sahip olabileceği düşünülmemelidir. Aslında, istisnasız tüm ankraj ve rotor tasarımları için, olukların mümkün olduğunca düz olması gerekir ve presleme işlemi sırasında presleme cihazındaki uygun eğimli kılavuz bıçaklar kullanılarak olukların gerekli eğimi elde edilir.
Çoğu zaman, fabrikada kesinlikle düz oluklu mil üretme yeteneğinin olmaması, bizi göbeği mile sabitlemek için çok daha pahalı diğer yöntemleri kullanmaya ve özellikle bu amaç için kama kullanmaya zorlar.
Oluklu miller için Düz kalıplı ve doğrusal çalışma stroklu makinelerin kullanılması gerekli değildir, ancak diğer tipte diş çekme ekipmanlarını başarıyla kullanabilirsiniz. Olukların haddelenmesinden sonra, miller, kısmen uzunlamasına, ancak esas olarak enine besleme ile merkezsiz taşlama makinelerinde taşlama işlemlerine tabi tutulur.
Aynı zamanda, boyutu üçüncü doğruluk sınıfı içinde tutmak ve bireysel dişlerin üst kısımlarını bir şekilde köreltmek için oluklu yüzeyin dış çapı da zorunlu olarak taşlanır, böylece aynı miktarda parazit ve pres bağlantısının yüksek kalitesi sağlanır. .
Merkezsiz işleme, merkezsiz işlemeye göre daha az işlem gerektirir ve özellikle tüm tedarik işlemleri ortadan kalkar - iş parçasının kesilmesi, uçlarının taşlanması ve merkezlenmesi. Bu durumda kullanılan ekipman da daha yüksek bir üretkenliğe sahiptir. Şaftı döndürmek için otomatik çubuk makinesi, işçi açısından çok kesicili torna tezgahından daha az bakım gerektirir. Her iki yöntemle elde edilen millerin kalitesi yaklaşık olarak aynıdır. Uzunluk boyunca birkaç adımlı millerin merkezsiz işlenmesiyle, vuruşlarının değerleri gerekli toleranslar dahilinde korunabilir.
Ayrıca ilginizi çekebilir:Üretme kademeli miller
Kademeli millerin imalatı için temel işlemler yapılırken, iş parçasının merkez deliklerinin yüzeyleri montaj tabanı olarak alınır. İş parçası yüzer bir ön merkeze kurulursa, kurulum tabanı iş parçasının ucu, ön merkezin ucuna bitişik olacaktır. Yüzer bir ön merkezin kullanılması, sol uçtan itibaren adımların uzunluklarını korurken konumlandırma hatasını ortadan kaldırır.
Kademeli mil boşluklarını işlemenin bireysel işlemlerini düşünün.
Kırpma ve merkezlemeyi sonlandırın. Kademeli millerin imalatında ilk teknolojik geçişler - teknolojik temellerin hazırlanması, ᴛ.ᴇ. uçları kırpmak ve merkezlemek. Şaft salma ölçeğine bağlı olarak, bu geçişler çeşitli ekipmanlar kullanılarak gerçekleştirilebilir.
Rijit olmayan şaftların iş parçalarını işlerken, muyluların sabit yatak altında ek olarak taşlanması veya taşlanması son derece önemlidir.
Boşlukların uçlarında, boşlukları elde etme yöntemi (damgalama eğimleri, talaşlar, dik olmama vb.) nedeniyle kusurlar vardır. Bu nedenle, kusurları gidermek ve çizimde belirtilen limitler dahilinde şaftın toplam uzunluğunu elde etmek için ilk işlem genellikle alın işlemedir. Bunun istisnası, 0,5 mm'lik bir uzunlukta doğruluk sağlayan otomatik kesme makinelerinde veya torna tezgahlarında elde edilen iş parçalarıdır.
İzin verilen uçlar, torna ve freze makinelerinde, freze-merkezleme, broş-merkezleme yarı otomatik cihazlarında işlenebilir. Büyük ölçekli ve seri üretimde yarı otomatik makineler kullanılmaktadır. Orta ve küçük ölçekli üretimde bu işlemler FC-1 ve FC-2 freze-merkezleme makinelerinde gerçekleştirilir. Delikler, merkez matkaplarla ortalanır. Deliklerin boyutları, iş parçalarının çapına göre atanır.
Tambur tipi bir freze-merkezleme yarı otomatik cihazı MR-76M'de (Şekil 3) işleme yaparken, ilk önce iş parçası kurulur (konum 1); sonra uçlar frezelenir (konum II) ve delikler ortalanır (konum III). Araçların her pozisyon için ayrı beslemeleri vardır. İşlemi bitirdikten sonra, aksesuarlarla birlikte tambur, pozisyonları değiştirmek için 120 ° açıyla döndürülür.
dönüm... Devir cisimleri gibi parçaların yüzeylerini elde etmenin ana yöntemi tornalamadır. Torna tezgahlarında kademeli millerin iş parçalarını kaba işlerken, haddelenmiş stok bir iş parçası olarak alındığında, bireysel adımların doğru işleme sırasını seçmek önemlidir.
Bir ucu kaba işlemeyi düşünün kademeli mil 100 mm çapında haddelenmiş ürünlerden (Şek. 4, a). Olası seçenekler Bu şaftın adımlarının işlenmesi Şekil 2'de gösterilmektedir. 4, b-d.
Pirinç. 3. İş parçasını freze merkezinde işleme şeması
yarı otomatik cihaz MR-76M
Pirinç. 4. Kademeli şaft boşluklarının kaba işleme şeması
İlk şemaya göre (Şekil 4, B) her ardışık aşama, önceki aşamayı aldıktan sonra ayrı ayrı işlenirken, kesicinin çalışma strokunun toplam uzunluğu Lp 400 mm olacak, rölanti hareketlerinin uzunluğu L x= 400 mm, kesme derinliği 11 ila 3,5 mm.
İkinci şemaya göre işlerken (Şekil 4, v) Lp= 550 mm ve L x= 550 mm; üçüncü şemaya göre - Lp= 650 mm ve L x= 650 mm; dördüncü şemaya göre - Lp= 800 mm ve L x= 800 mm.
Hem çalışma strokunun hem de kesicinin rölanti hareketlerinin en küçük uzunluğu, birinci şemaya göre işleme yapılırken elde edilir. Bu nedenle, bu şema en iyi performansı sağlar. Aynı zamanda, yetersiz makine gücü ile büyük bir kesme derinliği ile çalışın ( T= 3.5-11 mm) mümkün olmayabilir. Bu durumda, dördüncü şemaya göre çalışırken en yüksek verimlilik olacaktır.
Teknolojik sistemin sağlamlığı, kademeli şaftlar için herhangi bir işleme şemasının rasyonel seçimini de etkiler.
Şaft parçalarının boşluklarını döndürmek için makinelerin seçimi, üretim tipine ve ikincisinin tasarımına göre belirlenir. Bireysel üretimde, işleme genellikle üniversal makinelerde ve Program yönetimi(büyük şaftlar için). Küçük ve orta ölçekli üretimde taret torna ve programlı kontrollü makineler kullanırlar. Büyük ölçekli ve seri üretimde, şaftlar çok milli otomatik torna tezgahlarında, çok kesicili ve hidrokopi yarı otomatik cihazlarda işlenir.
Programlanmış kontrollü takım tezgahlarının kullanımı, yardımcı zamanı 12,5 ... 2 kat azaltır, ıskartaları azaltır (özellikle dolu millerin boşluklarını işlerken) ve çok istasyonlu hizmetin kullanılmasına izin verir.
Çok milli makinelerde, küçük uzunluktaki (200 mm'ye kadar) çubuk stoğundan şaft iş parçaları işlenir.
Çoklu kesici işleme, kesme uzunluğunu azaltarak ana sürede bir azalma sağlar. Adımlar artan derecede düzenlendiğinde, kademeli milleri işlerken kullanımı en uygundur. İşleme iki şekilde gerçekleştirilebilir (Şekil 5). Çok kesicili işlemenin avantajlarından tam olarak yararlanmak için tüm arabaların aynı anda çalışması zorunludur. Kütük olarak kullanıldığında, ödenek bölme yöntemine göre işleme yapılır. Z1, Z2, Z3(şek. 5, a), çünkü daha küçük çaplı alanlarda ödenek büyüktür. Kademeli boşluklardan millerin imalatında, uzunlamasına desteğin stroku uzunluk ile belirlenir. 1 en büyük adım (Şekil 5, B) veya l3 en küçük adım (Şekil 5, v). V son durum kalan adımları işlemek için birkaç kesici kurulur. Ayardaki kesicilerin sayısı, işlenmiş parçaların sertliği, makinenin gücü ve takım tutucu tasarımlarının karmaşıklığı ile sınırlıdır.
Pirinç. 5. Çoklu kesicide iş parçası milini işleme seçenekleri
yarı otomatik cihaz
Verimlilik açısından, çok kesicili tornalama, hidrokopi yarı otomatik makinelerde tornalamaya göre her zaman bir avantaja sahip değildir, bu da yüksek hazırlık ve son zaman ve zaman maliyetleri ile açıklanır. Bakım onarım... İşleme, azaltılmış kesme hızlarında gerçekleştirilir.
Hidrokopi yarı otomatik cihazlarda işleme, çok aletli işlemeye göre bir takım avantajlara sahiptir. Az sayıda kesici ve fotokopi makinesinin basit kurulumu, makinenin kurulum süresini azaltır, yüksek hızlarda işlemeye izin verir. Bu, bu makinelerin seri üretimde de kullanılmasına izin verir.
Hidrokopi makineleri (Şekil 6) rijit olmayan şaftların iş parçalarının ön ve finiş işlemesini, yüksek pürüzlülük gereksinimleri nedeniyle çok kesicili makinelerde uzunluk bölme yöntemini kullanarak işlenemeyen uzun şaft muylularına sahip iş parçalarının finiş tornalama işlemlerini gerçekleştirir. İşleme daha yüksek doğruluk sağlar (genellikle 0,05 ... 0,06 mm tolerans korunur). Üretilen hidrokopya makineleri modelleri, 320 mm çapa ve 1600 mm uzunluğa kadar şaftların işlenmesine izin verir.
Pirinç. 6. Bir hidrokopi makinesinde şaft boşluklarını işleme şeması
yarı otomatik cihaz
Mil taşlama... Ziraat mühendisliğinde "şaft" tipi parçaların iş parçalarını işlerken, çoğu durumda devrimin temel yapısal yüzeylerini oluşturma sorunu tornalama yöntemleriyle çözülebilir. Aynı zamanda millerin boyunlarını pürüzlülük ile 6 ... 8. doğruluk derecelerine göre işlerken Ra= 2,5 - 0,63 μm ve üstü, taşlama kullanmak daha ekonomiktir. Sertleştirilmiş mil yüzeylerinin işlenmesi için gereklidir. Güç taşlamanın gelişimi ile bağlantılı olarak, sert şaftların boyunlarının işlenmesi, ön çok kesicili tornalama yerine hemen silindirik taşlama makinelerinde gerçekleştirilir. Bu durumda, hassas damgalama yöntemleriyle elde edilen iş parçasından 2 ... 2.5 mm'lik bir kenar payı çıkarılır.
Mil işlemenin teknolojik rotasında, tasarım ve teknolojik özelliklere bağlı olarak taşlama işlemleri farklı bir yer alabilmektedir. Sertleştirilmiş miller işlenirken ısıl işlemden sonra taşlama işlemleri tamamlanır. Bu durumda, kireci gidermek ve ısıl işlem sırasında oluşan kusurları ortadan kaldırmak için merkez delikleri (temizleyerek, lepleyerek, zımparalayarak vb.) düzeltmek genellikle son derece önemlidir.
Isıl işlem görmemiş şaftların taşlanması, tüm frezeleme, delme ve diğer işlemler tamamlandıktan sonra gerçekleştirilir, bu da taşlanmış yüzeyleri daha sonraki işlemler ve nakliye sırasında hasardan korur. Yüzeyler kama kanalları, düzlükler veya delikler tarafından kesilmediğinden, tornadan sonra taşlama işleme doğruluğunu artırır. Bu sıralama, daha fazla işleme için kolaylık sağlar. Bitmiş mil muyluları, boyutları izin değerine dönüştürmeden ayar ve ölçüm tabanları olarak kullanılabilir.
Şaftlar, mevcut yöntemlerden biri kullanılarak silindirik ve puntasız taşlama makinelerinde taşlanır (Şekil 7). Uzunlamasına besleme yöntemi, önemli uzunluktaki yüzeyleri işlerken kullanılır. Küçük boyunlar daldırma yöntemi kullanılarak işlenir. Seri üretimde, bu yöntemle öğütme, genellikle belirli bir boyuta ulaşıldığında çapraz beslemeyi kapatan aktif kontrol cihazları kullanılarak otomatik bir döngüde gerçekleştirilir. Puntasız taşlama makinelerinde işlem yaparken, parçaların montajı ve sabitlenmesi için herhangi bir taban gerekli değildir. Bu makinelerdeki düz miller (pimler, akslar) boyuna besleme yöntemi kullanılarak taşlanmıştır. İşlem kolaylığı, kaba işleme ve yarı finiş için en basit taşıma sistemi ve aktif kontrol cihazları ile bu tür makinelerden otomatik hatların seri üretiminde montajına izin verir.
Pirinç. 7. Silindirik taşlama makinelerinde (a) ve merkezsiz taşlama makinelerinde (b) şaft boşluklarının işlenmesi için şemalar:
I - boyuna besleme yöntemiyle işleme; II - yöntemle işleme
derin taşlama; III - çapraz besleme yöntemiyle işleme
(kesme); IV - boyuna besleme yöntemiyle işleme; V - çapraz besleme yoluyla işleme
frezeleme ... Şaftların bir sırası var yapısal elemanlar dişlileri, burçları, kasnakları, zincir dişlilerini ve diğer parçaları takmak ve sabitlemek için gereklidir. Bu elemanlar arasında düzlükler, kama yolları, yivli yüzeyler bulunur. Küçük ölçekli ve bireysel üretimde, üniversal yatay ve dikey freze makinelerinde yassı ve kamaların frezelenmesi gerçekleştirilir. Segment anahtarları için kama yuvalarının frezelenmesi, yarıçapı yuvanın yarıçapına karşılık gelen disk yuvası kesiciler ile gerçekleştirilir. Kama yuvasının frezelenmesi genellikle parmak freze ile yapılır. Kesicinin oluğun girişinde dalmasını kolaylaştırmak için, oluğun genişliğine eşit çapta delikler açılır.
Büyük ölçekli ve seri üretimde, her strok için 0,2 ... 0,3 mm derinleşen bir kesici ile sarkaç besleme ilkesiyle çalışan, kama yuvalarının frezelenmesi için özel anahtar freze makineleri kullanılır. Bununla birlikte, delikleri delmek çok önemli değildir. Mil üzerinde birkaç kama yuvası varsa, işleme çok milli kama freze makinelerinde gerçekleştirilir. Seri ve seri üretimde şapkalar genellikle çok yerli fikstürlerde gerçekleştirilir. Çift taraflı şapkalar, bir dizi disk kesici kullanılarak çok milli makinelerde işlenir.
Şapkaları işlemek için en verimli süreç, harici broşlama makinelerinde broşlama olmalıdır.
Millerin spline yüzeyleri düz kenarlı, üçgen, tasarım gereği iç içedir. Düz kenarlı yivli yivli bağlantılar, manşonun iç ve dış çaplar boyunca merkezlenmesiyle, iç içe ve üçgen yivlerle - yan yüzeyler boyunca merkezlenerek gerçekleştirilebilir.
Kamalı bağlantılar için katı doğruluk standartları belirlenir ve teknik koşullar... Bu nedenle, yivlerin aralığının izin verilen sapmaları ve eşitsizliği ve yukarıda belirtildiği gibi eksene göre yer değiştirmeleri 0,02 ... 0,03 mm'yi geçmemelidir.
Mil kamaları frezeleme, planyalama veya keskileme, çekme ve haddeleme ile işlenebilir. Kama freze makinelerinde en yaygın frezeleme haddeleme yöntemidir. Aynı şekilde tüm profillerin kamaları diş açma (tip 561) ve dişli azdırma makinelerinde frezelenebilir. İşleme, bir veya iki (80 mm çapında) geçişte ocak kesicilerle gerçekleştirilir.
Bireysel ve küçük ölçekli üretimde, spline, kopyalama yöntemi ve profil kesiciler kullanılarak genel amaçlı freze makinelerinde işlenebilir. Mili belirli sayıda kama bölmek için evrensel bölme kafaları kullanılır.
Kamaların miller üzerinde planyalanması, kopyalama yöntemi kullanılarak çok kesicili planya kafaları ile gerçekleştirilir. Çoklu kesici kafalarla kopyalama yöntemi kullanılarak keskileme ve haddeleme yöntemiyle keskileme yapılabilir. Bu yöntemler genellikle kısa yivli yüzeylerin işlenmesi için kullanılır.
Frezelemeye kıyasla en üretken (5 ... 10 kez) broşlamadır, ĸᴏᴛᴏᴩᴏᴇ, takımın bir çıkışı olması için açık yivli kanalların işlenmesi için en kabul edilebilirdir. Radyal çıkışlı oluklar çekilirken, broş tasarımı daha karmaşık hale gelir (geri çekilebilir dişler).
Hemen hemen her boyutta yivli yüzeylerin imalatında en umut verici süreç soğuk yivli haddeleme işlemidir. Haddeleme, şeritler, rulolar, rulolar, çoklu rulo profil kafaları kullanılarak gerçekleştirilebilir. Deneysel verilere göre, bükülme sırasında haddelenmiş kamalar, kesme ile elde edilen kamalardan %10 ... 20 daha güçlüdür. Spline yüzeyleri elde etmek için düşünülen yöntemler, genellikle ek işleme gerekmeden gerekli kalitenin elde edilmesini sağlar.
Sertleştirilmiş millerin kamaları yarı otomatik kama taşlama makinelerinde taşlanır. Taşlama desenleri merkezleme yöntemine bağlıdır. Böylece, iç çapta merkezlenirken, yan yüzeylerin aynı anda taşlanmasıyla bir profil çarkı ile taşlama yapılabilir (Şekil 8, a). Dış merkezleme yan yüzeyler iki tekerlekle taşlanmıştır (şek. 8, B). Dış yüzeyin taşlanması, geleneksel silindirik taşlama makinelerinde gerçekleştirilir.
Pirinç. 8. Kamalar için taşlama şemaları
Delme delikleri. Millerin dönme yüzeylerinde veya uçlarında delikler elde etmek için delme işlemleri kullanılır. Millerin uçlarındaki eşmerkezli deliklerin işlenmesi, freze-merkezleme yarı otomatik cihazlarında hazırlık işlemleri sürecinde gerçekleştirilebilir. Bu durumda merkez matkabı yerine gerekli çapta burgulu matkap kullanılır. Derin delikler açarken (uzunluk çapın 5 katıdır), matkaplar kullanılır. derin delme tek taraflı kesme zorla besleme kesme alanına soğutma sıvısı Derin delme için yatay delme makinelerinde işleme yapılır. Deliklerin geri kalanı genel amaçlı delme makinelerinde iletken fikstürler kullanılarak işlenir. Verimliliği artırmak için birden fazla ataşman kullanılabilir.
Millerde çok sayıda delik açılması gerekiyorsa, modüler çok milli makinelerin kullanılması tavsiye edilir. Delikler, armatürlerin yapısında önceden işlenmiş oluklara, düzlüklere ve diğer elemanlara göre belirli bir açısal konum işgal ediyorsa, ek montaj elemanlarının (yaklaşık) eklenmesi son derece önemlidir. Aletin yönü için armatürlerin jig burçları ile donatıldığı söylenmelidir.
Bireysel ve küçük ölçekli üretimde herhangi bir alet kullanılmadan işarete göre delikler açılır. özel cihazlar... Orta ölçekli üretimde kullanabilirsiniz sondaj makineleri programlanmış. Cihazlar olarak, evrensel montaj cihazlarını (USP) kullanmak en ekonomik olanıdır.
diş açma... Şaftlar genellikle hem dış yüzeylerinde hem de deliklerde diş açmak için sağlanır. Deliklerde kılavuz çekme, çoğu durumda, tornalama işlemleriyle birleştirildiğinde (uç eşmerkezli deliklerde diş açarken) veya özel diş açma makinelerinde ayrı olarak kılavuzlarla gerçekleştirilir. Kılavuz çekme, vidayı sökmek için çalışma strokunun sonunda kılavuz dönüşünün tersine çevrilmesiyle ve tersine çevrilmeden gerçekleştirilir - musluğun işlenecek delikten geçişi ile. Kılavuzları makinelere sabitlemek için, iş parçası boyunca kendi kendine hizalanma olasılığı için uzunlamasına ve radyal yönlerde kılavuzun biraz hareket özgürlüğü sağlayan özel kartuşlar kullanılır.
İç dişlerin kesiciler, pafta kafaları, diş frezeleme ve diş çekme ile kesilmesi genellikle yeterince büyük diş çapları için kullanılır.
Mil işlemenin teknolojik rotasında dış dişlerin elde edilmesi farklı bir yer tutar. Diş açma, bir tornalama işleminde veya bağımsız bir işlemde bir geçiş olmalıdır. Bu işlemin teknolojik rotadaki yerini belirtmek için, iplik imalatının boyutlarını ve doğruluğunu, tornalama işleminin doygunluğunu, parça partisinin hacmini vb. dikkate almak son derece önemlidir. Aynı faktörler, aşağıdaki diş açma yöntemlerinden birinin seçimini belirler: kesiciler ve taraklarla diş açma; kesme kalıpları; kendiliğinden açılan diş açma başlıklarıyla kılavuz çekme; diş frezeleme; iplik taşlama; dişli haddeleme.
Kesiciler ve taraklarla diş açma, çoğunlukla tek seferlik ve küçük ölçekli üretimde vidalı torna tezgahlarında gerçekleştirilir. Rölantide harcanan büyük zaman ve yüksek hızlarda çalışamama nedeniyle süreç verimsizdir. Bu yöntem, standart olmayan dişleri, sonsuz vidaları, dikdörtgen dişleri keserken, diğer şaft yüzeyleriyle kesinlikle eş eksenli dişler elde ederken de kullanılır.
Yuvarlak kalıplarla diş açma, torna ve döner makinelerde, otomatik makinelerde ve yarı otomatik makinelerde yapılır. Ramları takmak için kullanılan tutucular, şahmerdan boyuna ve radyal yönlerde bir miktar hareket serbestliği sağlamalıdır. Kalıplarla kılavuz çekme, kalıpta parlatılmamış bir diş profilinin bulunması, düşük hızlarda çalışması ve kalıbın boşta oluşturulması için çok fazla zaman harcanması nedeniyle yüksek diş kalitesi ve üretkenliği sağlamaz.
Kendiliğinden genişleyen kılavuz çekme kafaları kullanılarak daha kaliteli dişler ve daha yüksek verimlilik elde edilir (Şekil 9). Kafa, cilalı çalışma yüzeylerine sahip dört yuvarlak veya prizmatik kalıp ile donatılmıştır. Strokun sonunda, kalıplar birbirinden ayrılarak kafanın hızlı bir şekilde geri çekilmesini sağlar. Bu tür kafalarla diş açma taret torna tezgahlarında, otomatik torna tezgahlarında ve yarı otomatik makinelerde yapılır. Diş açma ayrı bir işlem olarak planlanıyorsa cıvata kesme makineleri kullanılır.
Pirinç. 9. Kendinden genişleyen pafta kafası
Diş frezeleme, disk (uzun dişleri frezelerken) ve tarak (kısa dişleri frezelerken) kesicilere sahip diş freze makinelerinde gerçekleştirilir. Tarım makinelerinin milleri genellikle kısa dişlere sahiptir ve bu bağlamda, iplik işlemede yüksek verimlilik ve doğruluk sağlayan tarak kesicilerle frezeleme en yaygın şekilde kullanılır (Şekil 10).
Pirinç. 10. Bir tarak kesici ile kısa dişleri frezeleme şeması
Tarım makinelerinin parçalarının imalatında ipliklerin taşlanması pratikte kullanılmamaktadır. Bu yönteme duyulan ihtiyaç, çok yüksek hassasiyette dişlerin imalatında veya sertleştirilmiş parçalar üzerinde dişler yapılırken ortaya çıkabilir. Daha sonra tek dişli veya çok dişli çarklı diş taşlama makinelerinde taşlama yapılır.
İplik üretmenin en verimli yolu haddelemedir (dişli kafalarla kesmeye göre 10 ... 20 kat daha verimli). Yuvarlanarak, 6. derece doğruluktaki dişler elde edilir.
Büyük ölçekli ve seri üretimde şaft imalatında en yüksek verim, otomatik hatlar... Hatlar, tornalama (hidrokopi ve çoklu kesiciler) ve freze-merkezleme yarı otomatik makinelerinden, taşlama makinelerinden monte edilir ve taşıma ve yükleme cihazları, aktif kontrol ve engelleme araçları ile donatılmıştır.
Kademeli şaft imalatı - konsept ve çeşitleri. "Kademeli şaft üretimi" kategorisinin sınıflandırılması ve özellikleri 2014, 2015.
Bu TP aşağıdaki işlemleri içerir:
Son işleme, merkezleme
Mil muylularının tornalanması (tornalanması)
Ön taşlama
Freze kamaları
Freze kamaları
İplik işleme
Isı tedavisi
Merkez deliklerini düzeltme
Mil muylularının ince taşlanması
Kamalı taşlama
Diş Kalibrasyonu ve Çapak Alma
Kızarma
Kontrol
1.2.1. Mil ucu işleme ve merkezleme
Tek ve küçük ölçekli üretimde uçlar torna ve freze makinelerinde işlenir. Delme, tornalama, taret ve yatay delme makinelerinde merkezleme yapılır.Merkezleme, iki aletle (bükümlü matkap ve havşa açma) veya bir birleşik merkez matkapla yapılabilir. Matkabın konik açısı genellikle 60 0'dır, ancak şaftların ağır iş parçaları için 75 0 veya 90 0'a yükseltilir.
Bazı durumlarda, kesici aletler, şaftın uçlarında kazara hasar olması durumunda merkez deliği çentiklerden koruyan 120 0'lık bir açıyla ek bir pah gerçekleştirir.
Seri ve seri üretimde, üzerinde 2 ucun aynı anda frezelendiği (Şekil 1.3'te konum 2), ardından 2 delik ortalandığı (konum 3) freze-merkezleme yarı otomatik cihazları kullanılır.
Pirinç. 1.3. - Bir freze merkezleme yarı otomatik cihazda şaft işleme şeması.
1.2.2. Mil tornalama
Mil tornalama genellikle kaba işleme ve ince talaş işleme işlemlerini içerir. Kaba tornalama kaldırıldığında çoğu daha büyük kesme derinliği ve yüksek ilerleme hızı ile çalışma.Tek seferlik ve küçük ölçekli üretimde üniversal tornalarda tornalama yapılır. Kademeli milleri işlerken, çeşitli şemalar kesme, örneğin, Şek. 1.4.
Şek. 1.4., Kesici hareketinin toplam uzunluğunda , yani Şekildeki devreden daha az. 1.4., A. Ancak çalışma ve yardımcı pasajların sayısı daha fazladır.
Pirinç. 1.4. - Şaft tornalama şemaları
Bir kesim modeli seçerken, işlemin maksimum üretkenliğini ve minimum maliyetini elde etmeye çalışırlar. Bu durumda milin boyutları, boyutların ayarlanması ve kontrol edilmesi yöntemi, toleranslar ve diğer faktörler dikkate alınır.
Bazen, adımların çaplarında büyük bir farkla, mili mümkün olduğunca uzun süre zayıflatmamaya çalışırlar ve en küçük çaplı adımları en son öğütürler.
Uzun rijit olmayan milleri döndürürken sabit veya hareketli lunetler kullanılır. Sabit ara yatak, makine yatağına monte edilmiştir. Hareketli ara yatak destek üzerinde hareket eder ve kamları kesiciyi takip eder (Şekil 1.5., A).
İşlenen yüzeyin yüzey 2 ile hizalanmasını sağlamak gerekirse (Şekil 1.5., B), sabit kamlar yüzeydeki kesicinin önüne yerleştirilir.
Pirinç. 1.5. - Sabit bir dinlenme kullanarak şaft döndürme şeması
Şu anda küçük ölçekli üretimde CNC makineleri kullanılmaktadır. İşleme döngüsünü otomatikleştirmeyi, artırılmış kesme koşulları kullanmayı, üretkenliği artırmayı, çok istasyonlu hizmet uygulamayı, yüksek vasıflı işgücü eksikliğini azaltmayı, ıskartaları azaltmayı ve üretim için hazırlık süresini kısaltmayı mümkün kılarlar.
Büyük ölçekli ve seri üretimde, milleri döndürmek için çoklu kesici ve hidrokopi makineleri ve yarı otomatik makineler kullanılmaktadır. Genellikle 2 kaliperleri vardır - uzunlamasına ve enine, uçları düzeltmek, oluklar açmak ve şekilli tornalamak için kullanılır.
Kaliperler aynı anda çalışabilir. Çok kesicili makinelerde, gerekirse daldırma ve ardından uzunlamasına besleme ile tornalama kullanılır (Şekil 1.6., B).
Pirinç. 1.6. - Çok kesicili yarı otomatik bir cihazda mili döndürme şeması
Üniversal tornalara kıyasla, çok kesicili tornalar, çalışma strokunun uzunluğunu azaltarak, kesicilerin aynı anda çalışmasını sağlayarak ve ayrıca kesici değiştirme, takım tutucuyu döndürme ve kızağın rölanti hareketleri için gereken süreyi ortadan kaldırarak verimliliği artırabilir.
Hidro fotokopi makinesinin uzunlamasına desteğine, yalnızca bir şaft muylusunun boyutuna göre ayarlanmış 1 kesici yerleştirilmiştir. Boyutların geri kalanı bir fotokopi makinesi ve bir izleme sistemi ile elde edilir. Aynı zamanda, ölçüm sayısı azalır ve manuel beslemelerle çalışırken olduğundan daha yüksek bir kesme modu uygulanır.
Şaftlar bir veya birkaç çalışma vuruşunda döndürülürken, fotokopi makinesi ile tambur döndürülerek fotokopi makineleri otomatik olarak değiştirilir.
Şaftın bir hidrokopi makinesinde ve tek milli çok kesicili yarı otomatik bir cihazda işlenebileceği durumlarda, ekipman seçimi teknik ve ekonomik analiz temelinde yapılır.
Bu, aşağıdaki hususları dikkate alır:
Kesme uzunluğunun bölünmesiyle çok kesicili tornalamada, çalışma strokunun uzunluğu kopyalamaya göre daha kısadır.
Hidrokopi makineleri için kurulum ve yeniden ayarlama süresi, çok kesicili makinelere göre çok daha kısadır.
Çok kesicili makinelerdeki kesicilerin ve kesme modlarının sayısı, genellikle iş parçasının şekillendirilebilirliği ve yetersiz makine gücü nedeniyle sınırlıdır. Bir hidrokopi makinesinde, ana kesme hareketinin yüksek ilerleme hızlarıyla çalışabilirsiniz.
Yukarıdakilerle bağlantılı olarak, hidrokopyalama makinelerinin üretkenliği birçok durumda daha yüksektir.
Çoklu kesici doğruluğu, göreceli konum hatalarından ve eşit olmayan kesici aşınmasından etkilenir. Bir yüzeyi birkaç kesici ile işlerken, bölümlerin sınırlarında çıkıntılar oluşur. Hidrokopi makinelerinde bu hatalar yoktur, bu nedenle daha yüksek boyutsal doğruluk ve daha az pürüzlülük elde etmek mümkündür.
1.2.3. Dış silindirik yüzeylerin bitirilmesi
Dış silindirik yüzeylerin finisaj işlemleri için ince tornalama, taşlama, polisaj, lepleme, süper finisaj, merdanelerle tornalama vb.1.2.2.1. İnce tornalama
İnce tornalama, daha çok demir dışı metallerden ve alaşımlardan yapılmış iş parçalarının ince işlemesi için, daha az sıklıkla çelik ve dökme demirden yapılmış iş parçaları için kullanılır. Bu, taşlama çarkının "yağlanması" nedeniyle demir dışı alaşımların taşlanmasındaki zorluklarla açıklanmaktadır.Elmas, kompozit, sermet kesiciler ve sert alaşımlarla donatılmış kesiciler ile ana kesme hareketinin yüksek hızlarında, düşük ilerleme hızlarında ve kesme derinliklerinde işleme yapılır.
Hassas tornalama, 6 ... 7 kalite işleme hassasiyeti ve yüzey pürüzlülüğü elde etmenizi sağlar mikron.
İşleme performansı taşlamadan daha yüksektir. Büyük ölçekli ve seri üretimde, hassas tornalama için yüksek hassasiyetli ve titreşime dayanıklı özel yüksek hızlı makineler kullanılmaktadır.
1.2.2.2. Bileme
Dış silindirik yüzeyler için ana perdah yöntemidir. Taşlamanın avantajı, ısıl işlemden sonra iş parçasındaki hataları düzeltme yeteneğidir. Sıradan ince öğütme ile işleme, 1.2 ... 0.3 mikron yüzey pürüzlülüğü ile 6-7 doğruluk derecesine göre gerçekleştirilir.İnce öğütme, 5 kalite doğruluğu ve 0,16 ... 0,8 mikronluk bir pürüzlülük sağlar. Yüksek dönüş hızında, iş parçasının düşük dönüş hızında ve küçük kesme derinliğinde ince taneli bir tekerlek ile gerçekleştirilir.
Taşlama, uzunlamasına tekerlek beslemeli veya döndürme yoluyla dairesel ve merkezsiz taşlama makinelerinde gerçekleştirilir (Şekil 1.7.)
A - uzunlamasına beslemeli; B, C - döndürme yöntemi (yöntemi) ile
Pirinç. 1.7. - Silindirik bir taşlama makinesinde taşlama şeması:
Döndürme yöntemiyle taşlama daha verimlidir, silindirik ve şekilli yüzeyleri işlerken büyük ölçekli ve seri üretimde kullanılır.
Birden fazla boynun aynı anda taşlanması için, taşlama sırasındaki yardımcı zamanı azaltmak için birkaç daire ile çalışan özel makineler, taşlama işlemi sırasında iş parçalarının ölçülmesini sağlayan aktif kontrol cihazları ve makineyi otomatik olarak durduran cihazlar kullanılmaktadır. Belirli bir boyuta ulaşıldığında.
Puntasız taşlamada (Şekil 1.8.), İş parçası, biri (çapı büyük olan) taşlama ve diğeri önde gelen iki taşlama çarkı arasına yerleştirilir.
Pirinç. 1.8. - Merkezsiz taşlama şeması
Taşlama tekerleği 1, 20-35 m / s hızında, tahrik tekerleği 2 - 20-30 m / dak hızında döner. İş parçası 3 herhangi bir şey tarafından sabitlenmemiştir, ancak sürüş dairesine doğru yönlendirilmiş bir eğime sahip bir destek 4 tarafından desteklenmektedir.
İş parçasının tahrik çarkı ile yapışma kuvveti, taşlama çarkından daha fazladır. Bu, aşağıdaki nedenlerden kaynaklanmaktadır:
Azalan tekerlek hızı ile artan kesme kuvveti
Tekerlek ile iş parçası arasındaki sürtünme katsayısını artıran bir bağlantı üzerinde tahrik tekerleklerinin imalatı.
İş parçasının uzunlamasına besleme hareketi ile merkezsiz taşlamada, tahrik çarkının ekseni taşlama çarkının eksenine paralel değildir. Bu sayede özel bir besleme mekanizması olmadan iş parçası bir hızda hareket eder. nerede
- sürüş çemberinin dönüş hızı.
artan açı ile tekerlek eksenlerini geçerken işleme performansı artar, ancak yüzey kalitesi bozulur, bu nedenle genellikle
.
İşleme hassasiyetini artırmak için, delik içi taşlama bazen birkaç çalışma strokunda gerçekleştirilir. Büyük ölçekli ve seri üretimde, işleme, bir otomatik hatta bağlı birkaç makinede sırayla gerçekleştirilebilir.
Dalma yöntemine göre merkezsiz taşlama yapıldığında, tekerleklerin eksenleri çoğunlukla paraleldir. İlk olarak, tahrik çarkı taşlama çarkından geri çekilir ve iş parçası bir desteğe yerleştirilir, ardından tahrik çarkı iş parçasına getirilir ve belirli bir boyut elde edilene kadar enine besleme yapılır.
Merkezlerde taşlama ile karşılaştırıldığında, puntasız taşlama aşağıdaki avantajlara sahiptir:
Özellikle taret torna tezgahlarında ve otomatik makinelerde işlenen parçalar için önemli olan iş parçasını merkezlemeye gerek yoktur;
İşleme toleransları önemli ölçüde azalır, çünkü işlenmiş yüzeyin teknolojik bir temel olarak kullanılması nedeniyle, merkezleme hatasının tolerans üzerindeki etkisi ortadan kalkar;
Uzun ve ince millerin taşlanmasında dayanak kullanılmasına gerek yoktur;
Puntasız taşlama makinelerinin otomatikleştirilmesi ve otomatik hatta entegre edilmesi nispeten kolaydır;
Merkezlerde taşlamaya göre daha yüksek verimlilik sağlanır;
Basitlik nedeniyle makine kontrolü, öğütücünün ortalama bir yeterliliği ile yüksek doğruluk elde edilir;
Tekerlek aşınmasının neden olduğu işleme hatası, merkezlerde taşlamaya göre 2 kat daha azdır, çünkü tekerlek aşınması, yarıçapın değerine değil, iş parçası çapının boyutuna doğrudan yansıtılır.
1. Bu tür makinelerin kurulumu ve ayarlanması için harcanan zaman oldukça fazladır ve büyük iş parçası partileri için ödeme yapar. Bu nedenle, merkezsiz taşlama en çok otomotiv ve rulman endüstrilerinde kullanılır.
2. Çalışma yüzeyindeki kamalar, oluklar, delikler, boşluklar normal çalışmayı engeller ve hatta imkansız hale getirir.
3. Puntasız taşlama ile işlenmiş yüzeyin yuvarlaklığını sağlamak zordur.
4. Zemin yüzeyinin önceden işlenmiş diğer yüzeylerle hizalanmasını sağlamak zordur.
1.2.3.3. Parlatma ve Süper Finish
Yumuşak keçe, keçe veya bant tekerlekleri ile parlatma, yüzeyine ince taneli aşındırıcı toz ve yağlayıcı karışımı uygulanan aletin yüksek hızlarında gerçekleştirilir. Parlatma, düşük yüzey pürüzlülüğü sağlar (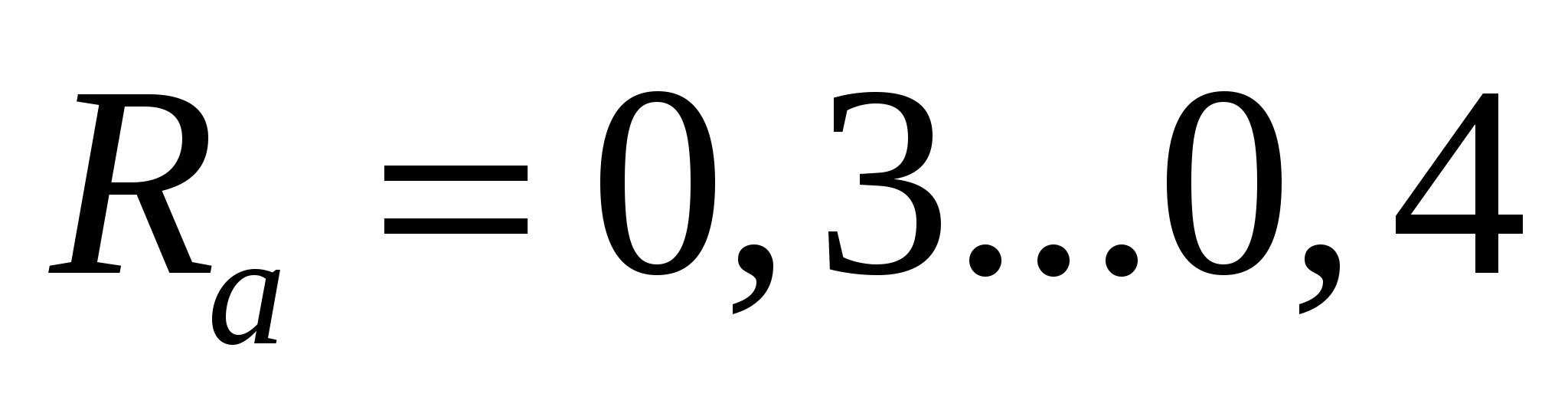
Superfinish (salınımlı çubuklarla finisaj), tekrarlanmayan bir iz ilkesini uygular; bu, hiçbir aşındırıcı tanesinin aynı yol boyunca iki kez hareket etmediği anlamına gelir. Bunun için, dönen iş parçasına ek olarak, düşük hızda (1-2,5 m / dak) ve çubukların uzunlamasına hareketi (Şekil 1.9.), Küçük bir genlikle dakikada 200 ila 1000 titreşim anlatılır. .
Salınım hareketleri, çubukların küçük tanecik boyutu ve düşük basınç nedeniyle iş parçasının küçük bir pürüzlülüğü sağlanır ( um).
Pirinç. 1.9. - Aşındırıcı çubuklarla şaft işleme şeması.
İşlem, kesme sıvısı kullanılarak gerçekleştirilir ve şu şekilde ilerler: ilk anda, çubukların işlenen yüzeyle temas alanı küçüktür ve çubuğun basıncının önemli olduğu ortaya çıkar, bu da yoğunluğa neden olur. metal çıkarma. Gelecekte, çubuklar çalıştırılır, basınç düşer ve kesme işlemi yoğunluğunu kaybeder.
Süper finisaj iş parçasının makrogeometrisini iyileştirmez, bu nedenle ön işleme parçanın doğru geometrik şeklini sağlamalıdır. Süperfiniş payı genellikle bırakılmaz.
1.2.4. İplik işleme
1.2.4.1. Kesiciler ve taraklarla diş açma
Torna tezgahlarında diş açarken iş parçası döndürülür ve kesici iş parçası ekseni boyunca devir başına diş adımına eşit bir ilerleme ile hareket ettirilir. Hatve doğruluğu, makinenin kinematik zincirinin doğruluğu ile belirlenir ve diş profilinin doğruluğu, kesiciyi bileme ve ayarlama doğruluğu ile belirlenir. Bu nedenle, işleme sırasında, tornacı genellikle ?????????????????????.Birkaç çalışma vuruşunda diş açarken, kesicinin çapraz beslemesinin hareketi, örneğin Şekil 2'de gösterilen şemalara göre gerçekleştirilebilir. 1.10. (a, b). (a) şemasını kullanırken, en iyi kalite işlenmiş yüzey ve şema (b)'ye göre çalışırken, kesim tabakasının şekli basitleştirilir, talaşların kesilmesi ve çıkarılması işlemi kolaylaştırılır. Bu nedenle bazen şema (b)'ye göre kaba işleme yapılır ve son katman şema (a)'ya göre kesilir.
Pirinç. 1.10. - İplik işleme için kesme kalıpları.
Bir kesici ile birkaç çalışma darbesinde diş açarken, kesici kenarı hızla körelir ve şekli bozulur, bu nedenle büyük hatveli - pürüzlü ve ince dişleri kesmek için 2 kesici kullanılması veya diş açma kalıpları kullanılması önerilir. Kalıplar, vuruş sayısını azaltarak, artan işleme verimliliği sağlar. Standart kalıpların dezavantajı, nokta-boş iş için kullanılamamasıdır; daha büyük çaplı muylulara bitişik diş açma için.
Tornalarda diş işleme genellikle aşağıdaki durumlarda gerçekleştirilir:
Aynı makinede daha önce açılmış iş parçalarına diş açarken, çünkü bu, yardımcı zamanı azaltır ve yüzeylerin göreli konumunun doğruluğunu artırır.
Hassas uzun vidalar yaparken.
Büyük çaplı dişleri veya standart olmayan hatve ve profilleri keserken, düşük üretim hacmi nedeniyle özel bir yüksek performanslı takım satın alınması uygun değilse.
Dikdörtgen dişleri keserken.
Ana kesme hareketinin hızını artırarak diş çekme verimliliğini artırmak, çoğu durumda kesiciyi hızlı bir şekilde geri çekmenin, dişin omuza bitişik olarak işlenmesinin zorluğundan dolayı zordur.
Büyük ölçekli ve seri üretimde, dişler genellikle çok geçişli işleme döngüsünü otomatikleştiren özel yarı otomatik makinelerde kesilir. Küçük ölçekli üretimlerde CNC makinelerinin kullanılması tavsiye edilir.
1.2.4.2. Dişi kesici kafalı freze dişleri
Dişi başlı diş açma, vidalı torna tezgahlarında ve diş açma makinelerinde gerçekleştirilir. Karbür kesiciler 1 (Şekil 1.11.) Kesme kafasına sabitlenir ve 150-450 m/dk hızla döner. Kafa, ipliğin yükselme açısına göre iş parçası eksenine bir açıyla monte edilir ve yavaş dönen iş parçasının her dönüşü için ekseni boyunca bir adım boyutunda hareket eder. En büyük etki, büyük dişleri işlerken elde edilir.Pirinç. 1.11. - Dişi başlı iplik kesme şeması.
1.2.4.3. Kalıplar ve kendiliğinden genişleyen başlıklarla kılavuz çekme
Torna-döner üzerine diş açarken ve modüler makineler kalıplar bir araç olarak kullanılabilir. Kalıp tutucular, aletin az miktarda serbestçe hareket etmesine veya dedikleri gibi, uzunlamasına yönde kendi kendine hizalanmasına izin verir. Bu, iş parçasının ekseni boyunca kalıp tutucunun hareket hızı, kalıbı iş parçası üzerine vidalama hızı ile çakışmadığında dişin kopmasını ortadan kaldırır.Kalıpların ana dezavantajı, diş açma işleminin bitiminden sonra onları vidalama ihtiyacıdır, bu da verimliliği ve işleme kalitesini azaltır.
Kendiliğinden genişleyen kesme kafalarıyla işleme yaparken, makyaj gerekmez ve üretkenlik önemli ölçüde artar.
1.2.4.4. Disk ve tarak (grup) kesiciler ile diş frezeleme
Disk kesicilerle frezeleme (Şekil 1.12.) Yeterince büyük çıktı hacimlerine sahip büyük dişleri işlemek için kullanılır. Bu durumda, işleme 1-3 çalışma vuruşunda gerçekleştirilir. İş parçası yavaşça döner ve ana hareket hızında dönen kesici, devir başına diş adımına eşit bir ilerleme ile ekseni boyunca hareket eder.Pirinç. 1.12. - Diş frezeleme şeması.
Tornalama ile karşılaştırıldığında, frezelemenin avantajı daha yüksek üretkenlik, çok istasyonlu bakım imkanı ve düşük vasıflı bir işçinin kullanılmasıdır.
İnce hatveli kısa dış ve iç dişler elde etmek için tarak (grup) kesicilerle frezeleme kullanılır.
Dişlerin disk kesici ile işlenmesinin aksine, tarak kesicinin ve iş parçasının eksenleri paraleldir (Şekil 1.13.). Kesicinin uzunluğu genellikle iş parçasının dişli bölümünün uzunluğundan 2-3 adım daha uzundur.
Pirinç. 1.13. - Bir tarak kesici ile diş frezeleme şeması.
İşleme başlangıcında döner kesici radyal olarak hareket eder ve iş parçasına diş profilinin derinliğine dalar. Bu durumda, iş parçasının 1 devri için, kesici diş adımı ile eksen boyunca hareket eder (besleme hareketi
). Frezeleme, iş parçasının 1.2 turunu alır. Ayrıca, işlemenin başlangıcında, kesiciyi daldırmak için ve sonunda - dalma işaretlerini temizlemek için 0,2 tur gereklidir.
1.2.4.5. Dişli haddeleme
İplik haddeleme, büyük ölçekli ve seri üretimde kullanılır. Yüksek üretkenliğe ek olarak, yöntem metalin uygun bir sertleştirilmiş yüzey yapısının elde edilmesini sağlar, çünkü malzemenin lifleri plastik olarak deforme olur ve kesilmez.İplik, düz kalıplar veya tırtıllı silindirler ile haddelenir.
Düz kalıplarda (Şekil 1.14.) Aynı profil ve yükselme açısına sahip düz bir diş (diş gelişimi) vardır. haddelenmiş bir iplikte olduğu gibi. İplik, kızağın bir çift vuruşunda sarılır. Dakikada çift vuruş sayısı 280'e ulaşır.
Pirinç. 1.14. - Kalıplarla iplik haddeleme modeli.
Tek taraflı radyal kuvvet nedeniyle torna tezgahlarında, taret torna tezgahlarında ve otomatik makinelerde tek rulo diş çekme kullanılır. Bu durumda, iş parçası bükülebilir.
Bu nedenle, radyal besleme hareketine sahip iki silindirli diş çekme daha yaygın hale gelmiştir (Şekil 1.15.).
Diş çekme, sabit bir merkez mesafesinde uzunlamasına beslemeli iki ila dört silindirle de yapılabilir. Üretkenlik açısından, silindirlerle haddeleme genellikle kalıplarla haddelemeye göre daha düşüktür.
Pirinç. 1.15. - Makaralı bir ipliği yuvarlama şeması.
2. Boyutlandırma talimatları. Örnekler: "* Referans için boyutlar"; "Belirtilmemiş yarıçaplar r3 "; "5º eğimler oluşturma".
3. Boyutların belirtilmemiş sınır sapmaları, örneğin, " H14, H14 , ± O14 / 2".
4. Tip dişlilerin kontrol parametreleri ile ilgili talimatlar: "Doğruluk göstergeleri seti, üretici tarafından GOST 1643-81'e göre oluşturulmuştur".
5. Çocuklarla birlikte köşeli parantez içinde boyutun işlenmesi. konum 3.
6. Birlikte uygulanacak detaylar.
Son iki paragraf, birlikte işlenen elemanlar için bir girişi gösterir (örneğin, mahfaza ve dişli kutusu kapağının yatak delikleri).
Ana yazıda, malzemeler standartların belirtilmesiyle verilmiştir: sıradan kaliteli çelikler (örneğin, St5, St6) - GOST 380-88'e göre, kaliteli karbon çelikleri (35, 45) - GOST 1050-88'e göre alaşım çelikler (40X, 30HGS) - GOST 4543-88'e göre, gri dökme demir (SCh15, SCh20) - GOST 1412-85'e göre, dövülebilir dökme demir (KCh 30-6) - GOST 1215-79'a göre.
Tasarım konuları yeterli sayıda ders kitabı ve referans kitabında belirtilmiştir. Çalışma çizimleri için gereksinimler de atölyede verilmektedir.
11.2. Şaft çizimleri
Çalışan bir çizim örneği kademeli milŞekil 'de gösterilmektedir. 51. Şaft basit bir tasarıma sahiptir, bu nedenle yapılmıştır bir projeksiyon, ana görüntüyü boşaltan öğelerin ve bölümlerin ayrıntılı görüntüleri ile desteklenir. İş parçasının boyutunu artıran dişli için baskı bileziği, kabul edildiği gibi yoktur. silindir merkezleme göbeğin uzunluğu çapından büyük olduğunda. Şaft, kaplin yarısını ve yatakları durdurmak için tasarlanmış basamaklara sahiptir. Uçlar, pahlar, filetolar veya dairesel oluklar ile sağlanır.
anahtar yolları milin bir tarafında simetri ekseni boyunca tasarlanmıştır. Birleştirme amacıyla aynı bölümün anahtarları kabul edilmiştir. Projeksiyon yarım daire uçlu oluklar parmak kesici ile imalatlarına karşılık gelir. Bu şekil, oluktaki anahtarın iyi stabilitesini sağlar. Bu üretim teknolojisi ile çalışmakta olan oluğun yan yüzeyleri yeterince yüksek pürüzlülük sınıfına sahiptir ( bir= 3,2 um). Çalışmayan yüzey
Pirinç. 51. Kademeli oluk milinin çalışma çizimi 1 ... 2 sınıf daha düşüktür. Anahtar yuvaları, bitişik uçlardan 5 ... 10 mm mesafede bulunur.
Her şey eksenel boyutlarüstte gösterilir, şekil toleransları ve yüzey sapmaları görüntünün üstünde ve altında gösterilir. çizim gösterir birleşik yöntem boyutlandırma. Kamaların, pahların ve olukların boyutları, adım boyutuna dahildir. Anahtarın uzunluğu en yakın uç yüze bağlanır.
Kamalı detay görünümleri ve detay görünümü gösterilir. dairesel alttan kesme... Dış bölümler, maksimum sapmalar, yüzey pürüzlülüğü ve kama yatağının boyutlarını gösterir. paralellik ve simetri toleransları oluğun çalışma kenarları. oluk derinliği TŞekil 1, şaftın büyük ölçüde silindirik bir yüzeyinden kesitte ince bir çizgi olarak gösterilen bir daire yayından gösterilmektedir.
Tüm eşleşme çapları aşırı sapmalarla gösterilmiştir. saplar için geçiş inişleri atayın ( k6, m6, n6 ), şok yükleri altında - garantili parazitli inişler ( P6, r6 ). Mil boyunları için dişli kutuları, garantili parazit sağlayan geçiş inişleri yapar ( j s6, k6, m6, n6 ) örneğin bir yatakla bağlantılı olarak, L0 /k6 . Dişli çarklar eşlerde şaft kafalarına bastırılır H7 /P6 (ana bağlantı - anahtarlı) veya H7 /r6 veya H7 /s6 (ana bağlantı - basın). huzurunda ara kollar ve halkaları çiftleşir H6 veya H7 .
Her şey silindirik yüzeyler Konjuge olmayanlar da dahil olmak üzere şaftlar, değişen gerilimlere maruz kaldıkları için yüksek bir pürüzlülük sınıfına sahiptir. Yüzey pürüzlülüğü için semboller verilmiştir. üst kısımlarşaft görüntüleri. Sapın birleşme yüzeyleri buna göre yapılır. bir= 2.5 ... 5 mikron; boyunların ve başın yüzeyi - bir= 1.25 ... 2.5 μm. Rulmanlar ve dişliler için omuzların uçları aşağıdakilere göre işlenir. bir= 2,5 mikron, bağlantının sonu - boyunca bir= 5 μm, mil uçları - ile bir= 10 um.
Tam metin araması:
Ana Sayfa> Özet> Sanayi, üretim
Öz
Ders projesi ödeve uygun olarak yürütülür ve 4 adet A1 formatında (parça çizimi, iş parçası çizimi, cihaz çizimi (teknolojik ekipman), teknolojik ayarlamalar) ve 52 sayfadan oluşan bir hesaplama ve açıklayıcı not içerir. yaprak, 4 şekil, 6 tablo. Çalışmada 8 kaynaktan yararlanılmıştır.
Ders projesinin konusu: "Şaft Mili" üretimi için teknolojik sürecin geliştirilmesi.
Çalışma sürecinde, ESTD'ye uygun olarak hazırlanmış bir rota-operasyonel teknolojik süreç tasarlandı.
Giriş 5
1 Parça 6'nın işleme sürecinin tasarımı
1.1 Parçanın hizmet amacı ve bunun için teknik gereksinimler 6
1.2 Çizimin teknolojik kontrolü ve üretilebilirlik analizi
yapılar 7
1.3 Üretim tipinin tanımı 9
1.4 Orijinalin boyutunun seçimi ve belirlenmesi için gerekçe
iş parçaları 14
1.5 Parça 17'nin rota işleme teknolojisini tasarlama
1.6 İşleme paylarının hesaplanması 19
1.7 İşletim Teknolojisi Tasarımı 23
1.7.1 Kesme koşullarının ve zaman oranlarının hesaplanması 23
1.7.1.1 Tasarım işlemi No. 010 "CNC Tornalama" 23
1.7.1.2 Tasarım işlemi No. 020 "Frezeleme" 30
1.7.1.3 Çalışma No. 025 "Cıvata kesme" 37
1.7.2 İşleme doğruluğunun hesaplanması 44
1.7.3 Ekipman seçimi 46
2 Teknolojik ekipman tasarımı 48
2.1 Parçayı özel alet 48'e kurmak için seçim ve gerekçe
2.2 Tasarımın teknik açıklaması ve çalışma prensibi
demirbaşlar 48
2.3 Sabitleme hesaplama şemasının geliştirilmesi ve mekanizmanın hesaplanması
kelepçe 48
Kullanılmış literatür listesi 51
Ek 52
Tanıtım
Şaftlar hizmet, tasarım, boyut ve malzeme açısından çok farklıdır. Buna rağmen, bir teknoloji uzmanı, mil üretimi için teknolojik bir süreç geliştirirken, aynı türden birçok sorunu çözmek zorundadır, bu nedenle, yapılan sınıflandırma temelinde oluşturulan tipik süreçlerin kullanılması tavsiye edilir.
Genel makine mühendisliğinde, yukarıdaki gruplardan çeşitli kombinasyonlarda kademesiz ve kademeli miller, dolu ve içi boş, düz ve yivli miller, dişli miller ve kombine miller vardır. Geometrik eksen şeklinde miller düz, krank mili, krank ve eksantrik (kam) olabilir.
Takım tezgahı yapımı da dahil olmak üzere makine mühendisliğinde en yaygın olanı, aralarında düz millerin hakim olduğu orta büyüklükteki çeşitli kademeli millerdir. ENIMS verilerine göre, makine mühendisliğindeki standart boyutlardaki kademeli millerin toplam sayısının %85'inden fazlası 150-1000 mm uzunluğundaki millerdir.
Şaft muyluları kama kanallarına, kamalara veya dişlere sahip olabilir. Eşleşen parçaları eksenel harekete karşı sabitlemek için dişleri, yaylı halkalar için oluklarla değiştirmek genellikle avantajlıdır. Bu, taşımayı ve montajı kolaylaştırır. Basamakların geçiş noktalarında oluklar veya filetolar yapılır. Fileto işleme daha zordur; bu nedenle, uygun olan yerlerde olukların sağlanması tercih edilir. Milin uçları pahlıdır. Kamalı miller, açık ve kapalı kamalı olabilir, ikincisi toplam standart boyutların yaklaşık %65'ini oluşturur. Tasarım gereği, spline'lar düz kenarlı ve kıvrımlı olabilir. Halihazırda, düz kenarlı kamalar (makine mühendisliğinde kullanılan standart kamalı millerin toplam sayısının yaklaşık %85-90'ı) hakimdir, ancak sarmal kamalar teknoloji açısından bir takım avantajlara sahiptir.
Uzunluk-çap oranı 15'ten az olan miller rijit olarak kabul edilir; 15'ten fazla bir oranla, millerin rijit olmadığı kabul edilir.
1. Parçanın işleme sürecinin tasarımı
1.1 Çizim ve çalışma koşullarına göre parça için hizmet amacı ve teknik gereksinimler
Detay - kademeli şaft. Kullanılan malzeme çelik 30X13 GOST 5632-72'dir. Şekillendirme yöntemi - dövme. Bitirdikten sonra mil montaja gönderilir.
Şaftın, Ra 1.25 parametresine (38js6; 40js6; 45js6; 32,2n6; 32n6) göre bir pürüzlülük ile 6. derece hassasiyete göre gerçekleştirilen beş muylusu vardır. Bu muyluların ikisinde, anahtarlı bir bağlantı vasıtasıyla dişli çarklar monte edilmiştir. Milin dış muyluları, dişlileri somunlarla eksenel hareketten korumak için M24 × 1.5-6g dişlidir.
Yüzeyler 40js6; 45js6 ve 32.2n6 mm, ısıl işlem sonucunda elde edilen 37 ... 43 HRC E. sertliğine sahiptir. Kalan yüzeylerin ısıl işleme (25..30 HRC E) maruz kalmaması için indüksiyon ünitesinde (HFC) üretilir.
Mil, yüksek alaşımlı, korozyona dayanıklı krom çelikten yapılmıştır. Bu, ürünün çalışma ortamından kaynaklanmaktadır.
1.2 Parça tasarımının üretilebilirliğinin analizi
Parçanın çizimi gerekli tüm boyutları içerir, işlenmiş yüzeyin pürüzlülüğü ve imalatlarının doğruluğu hakkında bilgi verilir.
Parçanın çizimi, parçanın tam bir resmini veren gerekli görünümleri içerir. Tasarım gereği, parçanın yüzeylerinin çoğu işleme için açık ve erişilebilir durumdadır.
Katsayılarla yüzeylerin niteliksel bir değerlendirmesini yapıyoruz:
1) Doğruluk K pt
A Çar - ortalama doğruluk kalitesi
A - karşılık gelen doğruluk kalitesi
N i - belirli bir doğruluk derecesinin yüzey sayısı
A 1 = 6 n 1 = 7
A 2 = 7 n 2 = 1
A 3 = 8 n 3 = 2
A 4 = 12 n 4 = 4
A 5 = 14 n 5 = 18
2) pürüzlülük K w
nerede
B cf - pürüzlülük parametresinin ortalama sayısal değeri
;
burada B, üzerindeki pürüzlülük parametrelerinin sayısal değeridir.
n ben w - pürüzlülüğü oluşturan yüzeylerin sayısı
B 1 = 1.25 n 1 = 6
B 2 = 6,3 n 2 = 26
3) malzeme kullanımı
m g = 5,6 kg - parça ağırlığı
m w - iş parçası ağırlığı = 7,84 kg
m atık - atık kütlesi
Böylece, her bakımdan GOST 14205-83'e göre parça üretilebilir.
1.3 Üretim tipinin tanımı
GOST 3.1108-74'e göre üretim türü, belirli bir süre içinde bir departman tarafından gerçekleştirilen veya gerçekleştirilecek tüm çeşitli teknolojik işlemlerin sayıya oranını gösteren Kz.o. işlemlerinin konsolidasyon katsayısı ile karakterize edilir. işlerin.
Kz.o. = Оi / Ря
burada ОI, farklı işlemlerin toplam sayısıdır;
Ря - çeşitli işlemleri gerçekleştiren birimin gerçek işçi sayısı.
GOST 14004-85'e göre, aşağıdaki üretim türleri sağlanmaktadır:
Bekar;
Seri;
Cüsseli.
Buna karşılık, parti üretimi büyük parti, orta parti ve küçük parti olarak alt bölümlere ayrılmıştır.
Hesaplama, ana işleme operasyonları ve metal işleme ekipmanı türleri dikkate alınarak yapılır.
İlk veri:
Yıllık ürün sürüm programı: N = 10000 adet
Üründeki parça sayısı: m=1.
İşletmenin çalışma şekli: Günde 2 vardiya.
Yaklaşık üretim türü orta partidir.
Sabitleme işlemlerinin katsayısını hesaplamak için parçayı işlemek için bir ön rota tanımlayacağız. Burada, tipik bir parça işleme teknolojik sürecine dayanarak, işlemenin ana şekillendirme işlemlerini seçeceğiz:
Frezeleme ve merkezleme. İş parçasının uçlarının frezelenmesi ve merkezlenmesi.
Cnc torna tezgahı. Dış yüzeylerin kaba ve ince tornalanması.
Frezeleme. Anahtar yolu frezeleme.
Cıvata kesici. M24 × 1.5-6g diş açma - iki yer.
Silindirik taşlama. Dış yüzeylerin taşlanması.
Hesaplama formülü kullanır
T sh-k = kim
1) Uçları frezeleyin.
Uçları ortalayın
2) Mil muylularını çevirin (kaba ve hassas tornalama)
3) Freze kamaları:
Parmak (kama yuvası) kesici
çalışma vuruşlarının sayısı nerede
Disk kesici
4) İpliği kesin:
5) Taşlama:
İşyerinin standart yük faktörünü belirleyin.
Tahmini makine sayısı:
nerede
n n - standart ekipman yük faktörü (seri üretim için n n = 0.75 alıyoruz).
N - üretim programı N = 10.000 adet.
F g - 4015 saat - geçerli yıllık ekipman çalışma süresi fonu
m pr = 1
m pr = 1
m pr = 1
m pr = 1
Ekipman yük faktörü:
Tek bir yerde gerçekleştirilen işlem sayısı:
Ekipman sayısı - 5
Operasyon sabitleme oranı:
10 Aynı anda üretime başlamak için bir partideki ürün sayısını belirleyin:
n= Na/254
a, gün cinsinden lansman sıklığıdır (biz a = 6)
n= 10000 * 6/254 = 237 adet
Partinin tamamını işlemek için vardiya sayısının belirlenmesi:
ben - işlem sayısı
ΣT sh-k = 27.25 dk
c = =3,39
c = 4 alıyoruz
Tüm vardiyalar sırasında ekipmanı yüklemek için gereken bir partideki ürün sayısını belirleyin:
= 279,48 adet n pr = 280 adet alıyoruz
1.4 Orijinal iş parçasının boyutlarının seçimi ve belirlenmesi için gerekçe
Az sayıda basamaklı ve çaplarda önemsiz farklılıklar olan miller, sıcak haddelenmiş veya soğuk çekilmiş bir çubuktan kesilmiş ve daha karmaşık bir konfigürasyona sahip ve çok sayıda basamaklı veya çap olarak önemli ölçüde farklı basamaklı parça boşluklarından yapılır - damgalama, çapraz haddeleme veya döner sıkıştırma ile elde edilen boşluklardan. Boşluğun seçimi teknik ve ekonomik hesaplamalarla gerekçelendirilmelidir.
Kitlesel ve büyük ölçekli üretimde, şaftlar, metalin verimli kullanılmasını (metal kullanım faktörü KIM = 0.65 ... 0.7) ve işlemenin emek yoğunluğunda önemli bir azalma sağlayan parça boşluklardan yapılır. CMM en az %5 artarsa, bir çubuktan bir parça kütük damgalama ile değiştirilir. Radyal küçültme ile elde edilen iş parçası, CMM = 0.85 ... 0.95 ile bitmiş parçaya konfigürasyon ve boyut olarak en yakın olanıdır.
Boş, kapalı bir kalıpta bir sıcak damgalama presinde elde edilir.
İş parçasının boyutlarının hesaplanması GOST 7505-89 "Dövme çelik dövmeler" uyarınca yapılır.
1.4.1. İlk veri.
Ekipman - sıcak damgalama presi.
İş parçası malzemesi - çelik 30X13.
Parça ağırlığı - 5,6 kg.
1.4.2. Dövmenin teknik özelliklerinin belirlenmesi.
1) Dövmenin hesaplanan kütlesini bulun =
, nerede
- parçanın kütlesi,
- GOST 7505-89'a göre belirlenen tasarım faktörü. = 1.4 (parça düz bir eksene sahip olduğu için).
elde ederiz = kilogram.
2) Doğruluk sınıfı - T2.
3) Çelik grubu - M3.
4) Dövmenin karmaşıklık derecesi, orana bağlı olarak belirlenir. , nerede
- dövmenin yazılı olduğu şeklin kütlesi. bizde =
, bu nedenle dövme işleminin karmaşıklık derecesi C1'dir.
5) Kalıp bağlantı yüzeyinin konfigürasyonu P'dir (düz).
6) Orijinal dizin 10'dur.
1.4.3. Hakedişlerin belirlenmesi ve hakedişler.
1) Boyutlar için ana ödenekler, mm:
1,5 - çap 40 mm, yüzey kalitesi Ra = 1,25 μm
1,2 - çap 42 mm, yüzey kalitesi Ra = 6,3 μm
1,6 - çap 46 mm, yüzey kalitesi Ra = 1,25 μm
1,2 - çap 53 mm, yüzey kalitesi Ra = 6,3 μm
1,4 - çap 39,5 mm, yüzey kalitesi Ra = 6,3 μm
1,5 - çap 32,2 mm, yüzey kalitesi Ra = 1,25 μm
1,4 - çap 24 mm, yüzey kalitesi Ra = 6,3 μm
1.1 - kalınlık 5 mm, pürüzlülük Ra = 6.3 mikron
1,2 - kalınlık 62 mm, pürüzlülük Ra = 6,3 mikron
1,2 - kalınlık 54 mm, pürüzlülük Ra = 6,3 mikron
1,7 - uzunluk 597 mm, pürüzlülük Ra = 6,3 mikron.
2) Kalıp parçasının yüzeyi boyunca yer değiştirme - 0,3 mm.
Düzlük ve düzlükten sapma - 0,5 mm
Damgalama önyargısı - 5
1.4.4. Dövme boyutları ve izin verilen sapmaları.
1) Dövmenin boyutları, mm:
Çap 24 + (1.4 + 0.3 + 0.5) × 2 = 28,4, 28,5 mm alıyoruz
Ç40 + (1.5 + 0.3 + 0.5) × 2 = 44.6, 45 mm alıyoruz
Ç42 + (1.2 + 0.3 + 0.5) × 2 = 46, 46 mm alıyoruz
Ç46 + (1,6 + 0,3 + 0,5) × 2 = 50,8 51 mm alıyoruz
Ç53 + (1,2 + 0,3 + 0,5) × 2 = 57, 57 mm alıyoruz
Çap Ç39.5 + (1.4 + 0.3 + 0.5) × 2 = 43,9 44 mm alıyoruz
Ç32.2 + (1.5 + 0.3 + 0.5) × 2 = 36.8, 37 mm alıyoruz
Kalınlık 5+ (1.1 + 0.3 + 0.5) × 2 = 8.8 9 mm alıyoruz
Kalınlık 62 + 1.2 + 0.3 + 0.5 = 64, 64 mm alıyoruz
Kalınlık 54 + 1.2 + 0.3 + 0.5 = 56, 56 mm alıyoruz
Uzunluk 597+ (1,7 + 0,3 + 0,5) × 2 = 602, 602 mm alıyoruz
2) Dış köşelerin yuvarlatma yarıçapı 2,5 mm'dir.
3) İzin verilen boyut sapmaları, mm:
Çap Ç28.5 çap Ç57
çap Ç45 çap Ç44
Çap Ç46 çap Ç37
Çap Ç51 kalınlık 9
Kalınlık 56 Kalınlık 64
uzunluk 602 .
İş parçasının çizimi bir A2 sayfasında sunulur
PenzGU 1.3-09.151001.123.002-ChZ
1.5 Bir parçayı işlemek için yönlendirme teknolojisi tasarımı
Tablo 1.
№ operalar |
Isim ve Özet |
teknolojik temeller |
Teçhizat |
Freze merkezleme Uçları frezele 2 tarafta orta |
İşlem görmemiş boyun yüzeyleri ve alın uçları 20 |
||
Cnc torna tezgahı Soldaki mili önceden keskinleştirin Sağdaki mili önceden bileyin Sonunda soldaki mili keskinleştirin Sonunda sağdaki mili keskinleştirin |
Aks ve uç yüz 1 (Aks ve popo 30) |
||
Çilingir |
çilingir tezgahı |
||
frezeleme Kama kanalını bir anahtar (parmak) kesici ile frezeleyin Kama yolunu bir disk kesici ile frezeleyin |
Boyun yüzeyi Ç40js6 ve uç yüz 30; Boyun yüzeyi Ç32,2n6 ve uç yüz 1; |
||
diş açma Diş M24 × 1.5-6g - iki yer |
Boyun yüzeyleri 32.2n6; 38js6 |
||
Çilingir çapak alma |
çilingir tezgahı |
||
Yıkama odası |
|||
Kontrol |
Kontrol plakası |
||
termal |
indüksiyon kurulumu |
||
silindirik taşlama Taşlama mili muyluları Ç38 mm; Ç40mm; Ç45 mm; Ç46mm; Ç32,2 mm; Ç32 mm |
Aks ve uç yüz 1 |
||
Çilingir Çapakları giderin, keskin kenarları köreltin |
çilingir tezgahı |
||
Yıkama odası |
|||
Kontrol |
Kontrol plakası |
||
koruma |
çilingir tezgahı |
Güzergah teknolojisinin son versiyonunu ekte verilen güzergah haritalarında GOST 3.1118-82'ye göre hazırlıyoruz.
1.6 Hesaplama ve analitik yöntemle ödeneklerin belirlenmesi
Bir yüzeyde ödenek, GOST 7505-89'a göre geri kalanı için hesaplama ve analitik yöntemle belirlenir.
40 js6 (± 0,008) mm boyutu için ödeneği hesaplıyoruz
Tedavi planı:
kaba tornalama
Tornalamayı bitir
Bileme
Merkezlerde taşlama ve taşlama yapılır, bu nedenle yüzeylerin konumunun sapması şuna eşittir:
Frezeleme-merkezleme işlemi için temel olarak kullanılan yüzey toleransı GOST 7505-89'a göre belirlenir:
Mekansal sapmaların artık değeri:
kaba işlemeden sonra
Bitirdikten sonra
Ödeneklerin minimum değerlerinin hesaplanması aşağıdaki formüle göre yapılır:
Minimum stok:
Ön tornalama için:
Son tornalama için:
Taşlama için:
Elde edilen verileri tablo 2'ye giriyoruz.
Yüzey işleminin teknolojik geçişleri |
Ödenek elemanları, μm |
Hesaplanan ödenek |
Tahmini boyut dp, mm |
Sınır boyutu, mm |
Ödeneklerin sınır değerleri, mikron |
|||||
2 Zmaks |
||||||||||
Boşluk |
||||||||||
ön tornalama |
||||||||||
son taşlama |
||||||||||
Bileme |
Tam boyuttan başlayarak "Tahmini boyut" (d p) sütunu eklenir:
En az sınır boyutu tolerans verilen ondalık kesir ile aynı işarete yuvarlayarak tanımlayın. En büyük sınırlayıcı boyut, en küçüğüne bir tolerans eklenerek bulunur.
Ödeneklerin değerini hesaplıyoruz:
Genel ödenekler ve
ara ödenekleri toplayarak belirleriz:
212 + 336 + 2960 = 3508 μm
258 + 434 + 4400 = 5092 μm
Hesaplamaların doğruluğunu kontrol edelim:
Kontrol doğrudur, bu nedenle hesaplama yapılır, doğru.
1. 40 js6 mm boyutu için ödenek ve toleransların düzenlenmesi.
1.7 İşletim teknolojisinin tasarımı
1.7.1 Kesme koşullarının ve zaman normlarının hesaplanması
1.7.1.1 Tasarım işlemi No. 010 "CNC tornalama"
İşlem CNC vidalı torna tezgahı modunda gerçekleştirilir. Dört kurulum için 16K20F3 (A ve B - kaba işleme, C ve D - bitirme), her birinde bir geçiş gerçekleştirilir. Bu işlemde, iş parçasını makineye yerleştirmek ve yerleştirmek için yüzer bir ön merkeze ve puntaya monte edilmiş bir döner merkeze sahip 2 çeneli bir ayna kullanılır.
Kesici takımlar, ISCAR tarafından üretilen ISO standardı torna takımlarıdır:
Kaba tornalama:
Sahibi: PCLNR 2020К-12
Ekle: CNMG 120408T-NR
burun yarıçapı r = 0,8 mm
alaşımlı levha IC 9025
V = 150..250 m / dak
S = 0.15..0.5 mm / devir
Dönüşü bitirin:
Sahibi: SVJCR 2020К-16
Ekle: VCMT 160404E-14
burun yarıçapı r = 0,4 mm
alaşımlı levha IC 9025
Üç kat TiN, AL 2 O 3, TiCN kaplama ile kimyasal biriktirme ile kaplanmış sert alaşım.
V = 250..400 m/dk
S = 0.12..0.25 mm / devir
Bu işlem için tüm hesaplamalar formüllere göre yapılır.
Dış boyuna ve enine tornalama için kesme hızı aşağıdaki formülle hesaplanır.
Kesme hızına göre Kv, bireysel katsayıların ürünüdür.
İLEmv
Knv - iş parçasının yüzeyinin durumunun etkisi (haddelenmiş ürünler için = 0.8; kaba işlemeden sonra = 1.0) Tablo 5,
kuv – kesici parçanın malzemesinin etkisi (= 1.9) tablo 6
KF – kesicinin planındaki ana açının etkisi (f95Å için = 0.7; f93Å için = 0.7) Tablo 18
Kaba tornalama (A ve B üniteleri):
Kesme derinliği t = 4 mm
İlerleme S = 0,5 mm / devir
İLE BİRLİKTE V= 350 sekme 17
m= 0,2
= 0,15
= 0,35
800 rpm makinenin pasaportuna göre en yakın değeri seçiyoruz
Kesme kuvvetini belirleyin:
P z =10 C P T x s y v n K P
Genel düzeltme faktörü cr K P = K mp K P K P K P K rp
K mp = 0.75 sekmesi 9
K J P= 0.89 sekmesi.23
K G P =1,1
K ben P =1,0
K rp
K P = 0,75*0,89*1,1*1=0,734
İLE BİRLİKTE P= 204 sekmesi 22
n = 0
P z =10*204*4 1 *0,5 0,75 *135,7 0 * 0.734 = 3561 N
Kesme gücünü hesaplıyoruz
bu = .
Lpx:
Lpiksel =Lres +y+ LEkle
nerede Lres -
LEkle -
y –
A'yı ayarlamak için:
Lres = 430 mm
Lekle +y= 14 mm
Lpiksel = 444 mm
Bu = 1.11 dakika
B'yi yüklemek için:
Lres = 187 mm
Lekle +y= 14 mm
Lpiksel = 201 mm
Bu = 0,503 dk
Bitirme tornalama (C ve D üniteleri):
Kesme derinliği t = 0,4 mm
İlerleme S = 0,25 mm / devir
Takım ömrü süresi T = 60 dak
İLE BİRLİKTE V= 420 sekmesi 17
m= 0,2
2000 rpm makinenin pasaportuna göre en yakın değeri seçiyoruz
Gerçek kesme hızı
Kesme kuvvetini belirleyin:
P z =10 C P T x s y v n K P
Genel düzeltme faktörü cr kesme kuvveti, bireysel katsayıların ürünüdür K P = K mp K P K P K P K rp
K mp = 0.75 sekmesi 9
K J P= 0.89 sekmesi.23
K G P =1,1
K ben P =1,0
K rp- sadece yüksek hız çeliği için dikkate alınır.
K P = 0,75*0,89*1,1*1=0,734
İLE BİRLİKTE P= 204 sekmesi 22
n = 0
P z =10*204*0,4 1 *0,25 0,75 *333,01 0 * 0,734 = 211,76 N
Kesme gücünü hesaplıyoruz
kw
kw
Ana makine işlem süresini tanımlayalım:
Bu =.
Çalışma strokunun uzunluğunu belirleyin Lpx:
Lpiksel =Lres +y+ LEkle
nerede Lres - kesme uzunluğu, işleme uzunluğuna eşittir.
LEkle - bazı durumlarda parçanın ayar ve konfigürasyon özelliklerinden kaynaklanan ek strok uzunluğu.
y – yaklaşma uzunluğu, dalma ve aletlerin taşması
B'yi yüklemek için:
Lres = 432 mm
Lekle +y= 6 mm
Lpiksel = 438 mm
Bu = 0.876 dk
G'yi ayarlamak için:
Lres = 196 mm
Lekle +y= 6 mm
Lpiksel = 202 mm
Bu = 0.404 dk
Operasyon için parça hesaplama süresinin belirlenmesi.
Seri ve seri üretim koşullarında zamanın teknik normları, hesaplama ve analitik yöntemle belirlenir. Seri üretimde parça hesaplama süresi standardı belirlenir:
Tsh-k = + Tşt,
nerede Tpz - hazırlık - operasyon için son zaman.
n – fırlatma parçaları partisinin boyutu; n= 280 adet
CNC torna tezgahlarında işleme sırasındaki birim zaman oranı şu şekilde tanımlanır:
T PC'ler = T Ö + T v + T obsl + T Lane
TÖ - ana teknolojik zaman
Tobl - teknik ve operasyonel bakım zamanı.
Tper- mola zamanları .
TELEVİZYON - yardımcı zaman:
T v = T bıyık + T ben + T hayvan + T itibaren
Tm.v. - boşta geri çekilmeler ve yaklaşmalar ile takım değişimi dahil olmak üzere, işleme bölgesinde takım tezgahının taretini hareket ettirmek için gereken tezgah-yardımcı süresi.
Tzo - parçayı sabitleme ve ayırma zamanı,
Parti -,
Tişört - bir parçayı ölçme zamanı,
T m.v. = T xx + T sc + T si
Teşekkürler- toplam boşta kalma süresi
tsk - kontrol programının çerçevelerini değiştirmek için toplam süre (ortalama olarak, bir çerçeveyi değiştirme süresi 1,5-2 saniyedir).
Tsi - Araçları değiştirmek için gereken toplam süre.
T PC'ler = T Ö + T bıyık + T itibaren + T hayvan + T xx + T sc + T si + T obsl + T Lane
Yüksüz toplam uzunluk -1862 mm
Hızlı hareket hızı - 2000 mm / dak
Teşekkürler= 1862/2000 = 0.931 dk
Tsi = 0.17 dakika
tsk= 1,5 dk
Tm.v.= 0.931 + 1.5 + 0.17 = 2.601 dk
2.893 + 0.4 + 2.601 = 5.894 dk
Tobsl + Tper= çalışma süresinin %12'si
Tobsl + Tper=5,894*0,12=0,707
Zaman normlarının elde edilen değerleri Tablo 3'te özetlenmiştir.
Tablo 3.
Kurulum A |
Kurulum B |
B'yi yükleyin |
Kurulum G |
||
T bıyık , dk |
|||||
T hayvan , dk |
|||||
T itibaren , dk |
|||||
T obsl + T Lane , dk |
|||||
T pz , dk |
|||||
T Ö , dk |
Tabloya dayanarak şunları elde ederiz:
T PC'ler =2,893+0,74+ 2,64 + 0,176 + 2.601 + 2.828 = 11.878 dk.
Tsh-k = + 11.878 = 11.942 dk.
1.7.1.2 Çalışma No. 020 "Frezeleme" tasarımı
İşlem, bir 6D91 kama freze makinesinde iki ayarda gerçekleştirilir. Bu işlem için, parçanın monte edildiği ve dış silindirik yüzey ve uç boyunca makineye dayanan özel bir cihaz kullanılması gerekir (cihazın montaj çizimi A1 formatında bir PenzGU sayfasında sunulur). 1.3-09.151001.123.005-СБ).
Kesici takım olarak özel kesiciler kullanılır:
A ayarı için - anahtar kesici 12 mm, kesici malzeme - yüksek hız çeliği R6M5
B montajı için - mantar kesici 48 mm ve b = 8 N8 mm, kesici malzeme - yüksek hız çeliği R6M5
Bu işlem için tüm hesaplamalar formüllere göre yapılır.
Kurulum A:
Parça fikstür üzerine monte edilmiştir ve 40.2'ye dayanmaktadır (çizim 40js6).
Bu geçişte kama, boyutlar ile frezelenir V=12,
T=
4.5H12. İşleme, 2,2 mm derinliğe kadar besleme ile iki geçişte "sarkaç" yöntemiyle gerçekleştirilir.
Freze derinliği t = 2,2 mm
Freze genişliği B = 12 mm
Kesici çapı D = 12 mm
Kesici diş başına ilerleme Sz= 0.18mm / diş
Kesicinin diş sayısı z = 2
Çalışma strokunun uzunluğunu belirleyin Lpx:
Lpiksel =Lres +y+ LEkle
nerede Lres - kesme uzunluğu, işleme uzunluğuna eşittir. Lres = 54 mm
LEkle - bazı durumlarda parçanın ayar ve konfigürasyon özelliklerinden kaynaklanan ek strok uzunluğu.
y – yaklaşma uzunluğu, dalma ve aletlerin taşması
Lekle +y=6 mm
Lpiksel = 54 + 6 = 60mm
Kesme hızını belirleyin V n,
dk ,
Kesme hızı için toplam düzeltme faktörü Kv, bireysel faktörlerin ürünüdür.
İLEmv- işlenen malzemenin kalitesinin etkisi (çelik için = 0.9) Tablo 3,
Knv
kuv –
T - alet dayanıklılığı; T = 80dk tab40;
İLE BİRLİKTE V= 12 tablo 39
m = 0,26
Q= 0,3
sen= 0
P= 0
Mil hızı:
n= 250 dakika
Kesme hızını netleştiriyoruz:
Dakika beslemesini belirleyin Sm, mm / dak:
Sm =Sz* z* n= 0.18*2*250 = 90mm/dak
Kesme kuvvetini belirleyin:
P z =10
düzeltme faktörü K mp kesme kuvveti hakkında
K mp = 0,3 sekme 9
İLE BİRLİKTE P= 82 sekmesi 41
sen = 1
Q= 0,86
P z =10
H
Kesme gücünü hesaplıyoruz
kw
kw
Ana makine işlem süresini tanımlayalım:
bu =
dk
B'yi yükleyin:
Parça fikstür üzerine monte edilmiştir ve Ç32.4'e dayanmaktadır (Ç32.2n6 çizimi).
Bu geçişte, boyutları olan bir kama yatağı frezelenir. V=8 +0,022 , T= 4 H12. İşleme mantar kesici Ç48 mm ve b = 8 H8 mm ile gerçekleştirilir, kesicinin malzemesi yüksek hız çeliği R6M5'tir.
Freze derinliği t = 4 mm
Freze genişliği B = 8 mm
Kesici çapı D = 48 mm
Kesici diş başına ilerleme Sz= 0,01 mm / diş
Kesicinin diş sayısı z = 12
Çalışma strokunun uzunluğunu belirleyin Lpx:
Lpiksel =Lres +y+ LEkle
nerede Lres - kesme uzunluğu, işleme uzunluğuna eşittir. Lres = 54 mm
LEkle - bazı durumlarda parçanın ayar ve konfigürasyon özelliklerinden kaynaklanan ek strok uzunluğu.
y – yaklaşma uzunluğu, dalma ve aletlerin taşması
Lekle +y=6 mm
Lpiksel = 54 + 6 = 60mm
Kesme hızını belirleyin V, m / dak, iş mili hızı n, dakika,
Kesme hızı için toplam düzeltme faktörü Kv, bireysel faktörlerin ürünüdür.
İLEmv- işlenen malzemenin kalitesinin etkisi (çelik için = 0.9) Tablo 3,
Knv - iş parçasının yüzeyinin durumunun etkisi (işlemden sonra = 1.0) Tablo 5,
kuv – kesici parçanın malzemesinin etkisi (= 1.0) tablo 6
T - alet dayanıklılığı; T = 60dk tab40;
İLE BİRLİKTE V= 72 tablo 39
m = 0,15
Q= 0,2
sen= 0,1
P= 0,1
Mil hızı:
Makinenin pasaportuna göre devir sayısını alıyoruz n= 1000 dakika
Kesme hızını netleştiriyoruz:
Dakika beslemesini belirleyin Sm, mm / dak:
Sm =Sz* z* n= 0.01*12*1000 = 120mm/dak
Kesme kuvvetini belirleyin:
P z =10
düzeltme faktörü K mp kesme kuvveti hakkında
K mp = 0,3 sekme 9
İLE BİRLİKTE P= 68.2 sekmesi 41
sen = 1
Q= 0,86
w= 0
P z =10
H
Kesme gücünü hesaplıyoruz
kw
kw
Ana makine işlem süresini tanımlayalım:
bu =
dk
Tsh-k = + Tsht,
nerede Tpz -
n – n= 280 adet
Tsht = + TV'ye ·k+ Tob.dan,
nerede O - ana zaman,
TELEVİZYON - yardımcı zaman:
Tv = Tus + Tzo + Tup + Tiz,
nerede Parti - parçanın takılması ve çıkarılması için zaman ,
Tzo -
Aptal -
Tişört - bir parçayı ölçme zamanı,
Tob.dan -
k k=1,85).
Tob.dan =T operasyon · %9
T operasyon = T Ö + T v · k
T operasyon = 2.833 + (0.094 + 0.068 + 0.12 + 0.62) 1.85 = 4.502 dk
Tob.başlangıç = 4.502 0.09 = 0.405 dk
Zaman normlarının elde edilen değerleri Tablo 4'te özetlenmiştir.
Tablo 4.
İsim |
Geçiş 1 |
Geçiş 2 |
|
Parti - |
|||
Tzo - |
|||
Sersem - |
|||
Tişört - |
|||
Tob.dan - |
|||
Tpz - |
|||
o- ana zaman, dk |
|||
Tsh-k =
+4,502+0,405
= 5,004 dakika.
1.7.1.3 025 "Diş açma" operasyonunun tasarımı
İşlem, 5D07 iplik kesme yarı otomatik cihazı ile iki ayarda gerçekleştirilir. Bu işlem için, bir cihaz kullanmak gerekir - parçanın monte edildiği ve dış silindirik yüzey boyunca makineye dayanan kendinden merkezleme çeneli bir mengene. Frezeleme işleminde kullanılana benzer özel bir cihaz kullanmak mümkündür.
Bir kesici alet olarak, kendiliğinden açılan bir vidalı kesme kafası kullanılır - GOST 21760 - 76'ya göre 4KA-70, aşağıdakilere göre yuvarlak bir tarakla
GOST 21761 -76, aşınmaya dayanıklı titanyum nitrür (TiN) kaplamalı yüksek hızlı çelik R6M5'ten yapılmıştır
Bu işlem için tüm hesaplamalar formüllere göre yapılır.
1) Kurulum A:
Parça fikstür üzerine monte edilir ve boyun Ç38js6 yüzeyine dayanır.
Bu geçişte iplik M24 × 1.5-6g olarak kesilir.
İlerleme (diş adımına eşit) S= 1,5 mm / devir
Diş çapı D = 24 mm
Kesme derinliği t = 1,3 mm
Lpx:
Lpiksel =Lres +y+ LEkle
nerede Lres - kesme uzunluğu, işleme uzunluğuna eşittir. Lres = 31 mm
LEkle - bazı durumlarda parçanın ayar ve konfigürasyon özelliklerinden kaynaklanan ek strok uzunluğu.
Y – yaklaşma uzunluğu, dalma ve aletlerin taşması
Lekle +y=3 mm
Lpiksel = 31 + 3 = 34 mm
Kesme hızını belirleyin V, m / dak, iş mili hızı n, dakika,
İLEmv
K T v
kuv –
T - alet dayanıklılığı; T = 120dk sekme49;
İLE BİRLİKTE V= 7.4 tablo 49
m = 0,5
Q= 1,2
Mil hızı:
Makinenin pasaportuna göre devir sayısını alıyoruz n= 160 dakika
Kesme hızını netleştiriyoruz:
Torku belirleyin:
m KP =10 C m NS Q S y K mp
düzeltme faktörü K mp kesme kuvveti hakkında
K mp = 0.85 sekme 50
İLE BİRLİKTE m= 0.046 sekmesi 51
Q= 1,1
m KP =10 0.046 24 1,1 1.5 1,5 0.85 = 23.69Hm
Kesme gücünü hesaplıyoruz
kw
kw
Ana makine işlem süresini tanımlayalım:
bu =
dk
2) B'yi yükleyin:
Parça fikstür üzerine monte edilir ve Ç32.2n6 boyun yüzeyi esas alınır.
Bu geçişte iplik M24 × 1.5-6g olarak kesilir.
İlerleme (diş adımına eşit) S= 1,5 mm / devir
Diş çapı D = 24 mm
Kesme derinliği t = 1,3 mm
Çalışma strokunun uzunluğunu belirleyin Lpx:
Lpiksel =Lres +y+ LEkle
nerede Lres - kesme uzunluğu, işleme uzunluğuna eşittir. Lres = 20,4 mm
LEkle - bazı durumlarda parçanın ayar ve konfigürasyon özelliklerinden kaynaklanan ek strok uzunluğu.
y – yaklaşma uzunluğu, dalma ve aletlerin taşması
Lekle +y=3 mm
Lpiksel = 20,4 + 3 = 23,4 mm
Kesme hızını belirleyin V, m / dak, iş mili hızı n, dakika,
Kesme hızı için toplam düzeltme faktörü Kv, bireysel faktörlerin ürünüdür.
İLEmv- işlenmiş malzemenin kalitesinin etkisi (çelik için = 0.8) tablo 50,
K T v - kesilen ipliğin doğruluğu (tam = 0.8) tablo 50 dikkate alınarak,
kuv – kesme parçasının malzemesinin etkisi (= 1.0) tablo 50
T - alet dayanıklılığı; T = 120dk sekme49;
İLE BİRLİKTE V= 7.4 tablo 49
m = 0,5
Q= 1,2
Mil hızı:
Makinenin pasaportuna göre devir sayısını alıyoruz n= 160 dakika
Kesme hızını netleştiriyoruz:
Torku belirleyin:
m KP =10 C m NS Q S y K mp
düzeltme faktörü K mp kesme kuvveti hakkında
K mp = 0.85 sekme 50
İLE BİRLİKTE m= 0.046 sekmesi 51
Q= 1,1
m KP =10 0.046 24 1,1 1.5 1,5 0.85 = 23.69Hm
Kesme gücünü hesaplıyoruz
Ana makine işlem süresini tanımlayalım:
bu =
dk
3) İşlem için parça hesaplama süresinin belirlenmesi.
Seri ve seri üretim koşullarında zamanın teknik normları, hesaplama ve analitik yöntemle belirlenir. Seri üretimde parça hesaplama süresi standardı belirlenir:
Tsh-k = + Tsht,
nerede Tpz - hazırlık - operasyon için son zaman.
n – fırlatma parçaları partisinin boyutu; n= 280 adet
Tsht = + TV'ye ·k+ Tob.dan,
nerede O - ana zaman,
TELEVİZYON - yardımcı zaman:
Tv = Tus + Tzo + Tup + Tiz,
nerede Parti - parçanın takılması ve çıkarılması için zaman ,
Tzo - parçayı sabitleme ve ayırma zamanı,
Aptal - makine kontrol teknikleri için zaman,
Tişört - bir parçayı ölçme zamanı,
Tob.dan - işyerine servis zamanı ve dinlenme ve kişisel ihtiyaçlar için molalar,
k- seri üretimi dikkate alan katsayı ( k=1,85).
Tob.dan =T operasyon %7
T operasyon = T Ö + T v · k
T operasyon = 0,24 + (0,094 + 0,068 + 0,12 + 0,55) 1,85 = 1,78 dk
Tob.başlangıç = 1,78 0,07 = 0,125 dak
Zaman normlarının elde edilen değerleri Tablo 5'te özetlenmiştir.
Tablo 5.
İsim |
Geçiş 1 |
Geçiş 2 |
|
Parti - bir parçanın takılması ve çıkarılması için süre, min |
|||
Tzo - bir parçayı bağlama ve ayırma süresi, min |
|||
Sersem - makine kontrol teknikleri için zaman, min |
|||
Tişört - bir parçayı ölçme zamanı, min |
|||
Tob.dan - işyerine servis zamanı ve dinlenme ve kişisel ihtiyaçlar için molalar, min |
|||
Tpz - hazırlık - son süre, min |
|||
o- ana zaman, dk |
|||
Aleti alma ve iade etme süresi, min |
Tabloya dayanarak şunları elde ederiz:
Tsh-k = +0,24+0,125 = 0.46 dakika.
1.7.2 İşleme doğruluğunun hesaplanması
İşleme doğruluğunun hesaplanması, son tornalamanın toplam hatasının belirlenmesinden ve bunu 9. doğruluk derecesi 40.266 h9 (-0.062) uyarınca boyut toleransı ile karşılaştırmaktan oluşur.
Toplam işleme hatası formülle hesaplanır
işleme sırasında ortaya çıkan hatalar nerede;
- teknik sistemin boyuta ayarlanmasında hata.
1. Takımın boyutsal aşınmasından kaynaklanan işleme hatasını belirleyin
Bir grup iş parçasını işlerken takımın izin verilen boyutsal aşınmasının tablo 29'unu kullanarak şunları belirleriz:
20 mikron
2. Kuvvetin tutarsızlığından kaynaklanan elastik sehimleri tanımlayalım.
Yüzey işlemi makine kamlarında kenetleme ile yapıldığından burada aşağıdaki formül geçerlidir.
uyma eşittir
μm / kN
Radyal kuvvet formül tarafından tanımlanan
nerede mm;
mm
Kesme hızı değeri: m/dak.
Tablo 22'den şunu buluyoruz: İLE BİRLİKTE P = 204; n = 0; x= 1,0; Y= 0,75
Kesme kuvveti için düzeltme faktörü değeri
K P =0,734
Kesme hızını hesaplıyoruz ve radyal kuvveti belirliyoruz
Elastik sapmaları tanımlayın
3. Boyut için teknik sistemi ayarlama hatasını belirleyin
mikron.
4. Termal deformasyonlar formülle belirlenir
,
mikron
5. Formül ile tanımlarız
,
mm,
mm;
mikron.
Toplam işleme hatası
Toplam hatayı, 62 mikron olan 40.266 h9 boyut toleransıyla karşılaştırıyoruz.
62 μm> 55,5 μm
Sonuç: işleme hassasiyeti korunur.
1.7.3 Ekipman seçimi
İşletmeler, teknolojik rotayı, mümkünse, tüm rotanın bir atölye ekipmanı için gerçekleştirileceği şekilde planlamaya çalışırlar. Bunun nedeni, yönlendirme sürecinin bir bölümünü başka bir atölyeye taşırken birçok belgeyi tamamlama ihtiyacıdır.
Öngörülen teknoloji bu kuralı karşılar. Tedarik operasyonu dışında tüm operasyonları atölyenin tek bir bölümünde gerçekleştirilir.
Belirli bir ekipman modelinin seçimi boyut, hassasiyet ve güç kriterlerine göre yapılır.
Ekipmanın operasyonlara göre dağılımı Tablo 6'da özetlenmiştir.
Tablo 6.
Makine adı |
kesici alet |
Ek ve yardımcı araç |
Ölçüm aleti |
|
Freze merkezleme yarı otomatik cihaz |
Matkap 4 P6M5 GOST 14034-74 Matkap merkezi. 2317-0107 (f4.00) GOST 14952-75 Parmak freze Ø 100 T5K10 GOST 24359-80 Freze (f100) 2214-0001 T5K10 45 ° GOST 24359-80 |
|||
Vidalı torna tezgahı CNC 16K20F3 ile |
Uçlu düz kesici PCLNR 2020К-12: CNMG120408T-NR Düz kesici SVJCR 2020К-16 |
Chuck 2 x çene |
Mikrometre MK 25-1 GOST 6507-78 Sürmeli kumpas ШЦ-I-125-0,1-1 GOST 166 Pürüzlülük örnekleri GOST 9378-75 |
|
Kama freze makinesi 6D92 |
Özel anahtar kesici Ç12mm P6M5 Freze (f12) 2234-0367 N9 GOST 9140-78 Özel mantar kesici Ç48 mm ve b = 8 Н8 Р6М5 |
özel cihaz |
Sürmeli kumpas ШЦ-I-125-0,1-1 GOST 166 |
|
İplik kesici yarı otomatik cihaz 5D07 |
Tarak 2671-0773 GOST 21761-76 |
Kafa 2681-0023 GOST 21761-76. Kendinden merkezlenen çene mengenesi |
Dişli halka М24 × 1.5. Pr ve DEĞİL. |
|
Silindirik taşlama makinesi 3M151 |
Taşlama taşı PP300 × 30 × 24А40PS1-С2 6К5 50 m / s 1kl.А GOST 2424-83 |
Orta ön, arka GOST 13214-79 Kelepçe GOST 16488-79 |
Zımbalar Cad. ve yok. Pürüzlülük örnekleri GOST 9378-75 |
Matkap 2300-6173 (f5.00) GOST 10902-77
Sürmeli kumpas ШЦ-I - 250-630 - 0.05-1 GOST 166-89
Sürmeli kumpas ШЦ-I - 125 - 0,05-1 GOST 166
Sürmeli kumpas ШЦ-I - 125 - 0.10-1 GOST 166
Stand ShM-I-8 GOST 10197-70
Gösterge ICh02 cl. 1 GOST 577-68
İletki tipi 1-2 GOST 5378-88
Mikrometre MK50-1 GOST 6507
Mikrometre MK25-1 GOST 6507-90
Kesim için braket 061 OST 95 1960-78. çap
Zımba CP 50 GOST 11098-75
Halka 8211-0094 6g (M24 X1,5-PR) GOST 17763-72
Halka 8211-1094 6g (M24 X 1,5-HE) GOST 17764-72
Fiş 8133-0630 (f5) H14 GOST 14807-69
2. Teknolojik ekipman, ölçü ve kesici takımların tasarımı
2.1 Bir fikstüre bir parça takmak için seçim ve gerekçe
Parçanın çiziminden, kama yolunun frezelenmesi için parçayı makineye tutturmak için özel bir cihaz kullanılması gerektiğini takip eder. İçinde iş parçası bir prizma ve iki desteğe dayanmaktadır. Fikstür büyük ölçekli üretimde kullanıldığı için hızlı bir kenetleme cihazı ile donatılmalıdır. Sıkıştırma mekanizmasının pnömatik tahriki bu gereksinimleri karşılar.
2.2 Tasarımın teknik açıklaması ve cihazın çalışma prensibi
Cihaz bir gövde, bir kurulum prizması, bir kol sıkma cihazından oluşur. Tek etkili pistonlu pnömatik silindir, pnömatik silindirin üst kısmına basınçlı hava beslendiğinde, çubuklu piston alçaltıldığında ve bir manivelalı şanzıman vasıtasıyla parçayı bir kelepçe ile, yani parçayı preslerken tahrik olarak kabul edilir. sabittir. Üst boşluğa basınçlı hava beslemesi durdurulduğunda, kenetleme mekanizmasına takılan yaylar kelepçeyi kaldırır ve bununla birlikte rotlar ve piston kolu yukarı kalkar ve parça serbest kalır.
2.3 Sabitleme hesaplama şemasının geliştirilmesi ve sıkıştırma mekanizmasının hesaplanması
İş parçası, cihazın montaj elemanlarına dayanır ve Q kuvveti ile bir kelepçe ile bunlara bastırılır ve kesme kuvveti P o dik yönde etki eder. Kesme kuvveti P o, fikstürün destek yüzeyi ile parçanın alt referans düzlemi arasındaki ve ayrıca parçanın üst düzlemi ile sıkıştırma yüzeyi arasındaki sürtünme kuvveti T tarafından karşılanır.
Pirinç. 4
Y eksenine göre iş parçasına etki eden tüm kuvvetler için denge denklemini oluşturalım:
ΣF yi = Q - 2Rsina / 2 = 0
Gerekli sıkıştırma kuvveti şu ifadeden belirlenir:
kР ® = Qf 1 + 2Rf 2
, nerede
k, kelepçenin güvenlik faktörüdür.
k 0 = 1.5 - garanti edilen güvenlik faktörü.
k 1 = 1.0 - stoktaki değişimi dikkate alan katsayı
k 2 = 1.4, takım kör olduğunda kesme kuvvetindeki artışı hesaba katan bir katsayıdır.
k 3 = 1.2 - kesintili kesme sırasında kesme kuvvetindeki artışı dikkate alan katsayı
k 4 = 1.0 - sıkıştırma kuvvetlerinin sabitliğini dikkate alan katsayı
k 5 = 1.0 - sadece elle çalıştırılan sıkıştırma mekanizmalarını karakterize eden katsayı
k 6 = 1.0, iş parçasını döndürme eğiliminde olan bir momentin varlığını hesaba katan bir katsayıdır.
bir = - prizma açısı
f 1 = f 2 = 0.15
Sıkıştırma mekanizmasının hesaplanması:
Sürücünün boyutunu belirleyin:
r ve =0,785 NS 2 PH
p = 0,4 N / m 2 = 4 kgf / cm 2 - basınçlı havanın özgül basıncı;
=0,7.
Ortaya çıkan çapı en yakın değere yuvarlayın.
Gövde çapı: d = 0.25D = 0.25 * 100 = 25 mm.
Kullanılmış literatür listesi.
A.F. Gorbatsevich. Makine mühendisliği teknolojisinde ders tasarımı. Minsk: "Lise", 1983.
A.G. Kosilova ve R.K. Meshcheryakov. Bir makine mühendisinin teknoloji uzmanının el kitabı. İki ciltte. Cilt 2. M.: "Makine mühendisliği", 1985.
"Metallerin kesme modları". tarafından düzenlenen el kitabı Yu.V. Baranovski... M. "Makine Mühendisliği", 1972.
A.G. Kosilova ve R.K. Meshcheryakov. Bir makine mühendisinin teknoloji uzmanının el kitabı. İki ciltte. Cilt 1. M.: "Makine Mühendisliği", 1985
A.K. Goroshkin. Metal kesme takım tezgahları için ataşman. El Kitabı 7. baskı, gözden geçirilmiş ve tamamlanmıştır. Moskova: Makine Mühendisliği 1979
"Metal kesme": Düzenleyen el kitabı AA Panova... - M.: Makine Mühendisliği, 1988.
B.L. Bespalov, L.A. Glazer, I.M. Kolesov Makine mühendisliği teknolojisi M., "Makine mühendisliği", 1973
Otomatik makine mühendisliği teknolojisinin tasarımı: Ders kitabı. makine mühendisliği için. uzman. üniversiteler / ONLARA. Baranchukova, A.A. Gusev, Yu.B. Kramarenko ve diğerleri; ed. Yu.M. Solomentseva... - 2. baskı, Rev. - M.: Daha yüksek. okul, 1999
benzer makaleler